- 8 (495) 7487600
- 8 (495) 7487600
- 8 (925) 5552040
- 8 (925) 5552040
- Напишите нам
- Обратный звонок
Интернет магазин оборудования насосной, отопительной и водонагревательной техники №1
Производство поверхностей нагрева. Изготовление поверхностей нагрева котлов
Изготовление поверхностей нагрева — часть 1
Поверхности нагрева являются основной частью любого котла как по своему весу, так и по доле трудоемкости при изготовлении его на заводе.
Под поверхностями нагрева здесь понимаются трубные элементы, работающие под давлением и образующие поверхности нагрева пароперегревателя, водяного экономайзера, топочных экранов, а также водо- и пароперепускные трубы.
Применяемые материалы
Змеевики пароперегревателя и водяного экономайзера, как правило, изготавливаются из труб диаметром 25-38 мм, трубы экранов обычно имеют диаметр 60 мм, а водо- и пароперепускные трубы – диаметр 108-133 мм.
Марка применяемой стали и толщина стенки трубы зависят от тех параметров, при которых работает данная труба. Для труб экрана и змеевиков водяного экономайзера, а также водоопускных труб в подавляющем большинстве случаев применяют сталь 20, для изготовления змеевиков пароперегревателя и пароперепускных труб служат стали марок: 20, 12ХМФ, 12Х1МФ, 15ХМ, 12Х2МФСР, Х18Н9Т, Х18Н12Т и им подобные.
Трубы диаметром от 57 до 133 мм изготовляются горячекатаными. Трубы диаметром от 10 до 108 мм холоднотянутыми, холоднокатаными и теплокатаными. Горячекатаные трубы поставляются длиной не более 12 м, холоднокатаные и теплокатаные трубы могут быть длиной до 18 м.
Трубы внутри и снаружи защищается от коррозии на время транспортировки и хранения в течение 6 месяцев. Защитное покрытие не должно содержать масел.
Если контроль труб физическими методами выполнен в достаточном объеме, то гидравлическое испытание на заводе-изготовителе можно не производить, но и в этом случае завод гарантирует, что трубы выдержат необходимое давление.
Трубы поставляются партиями. Под партией труб понимаются трубы одной марки стали, одной плавки, одного размера, прошедшие термическую обработку в одинаковых условиях. Количество труб в одной партии – не более 200 штук. На каждом конце трубы диаметром 25 мм и более, толщиной стенки не менее 3 мм на расстоянии 200-300 мм от конца клеймом наносится маркировка: марка стали и номер партии. Концы труб диаметром до 133 мм плотно закрываются пластмассовыми колпачками.
Трубы поступают на котлостроительный завод в железнодорожных вагонах без специальной упаковки, кроме труб аустенитного класса, которые упаковываются в деревянные ящики.
Подготовка труб к производству
К надежности работы поверхностей нагрева предъявляются очень жесткие требования, так как любой случай нарушения их нормальной работы ведет к останову котла, что связано с большими материальными потерями, особенно на котлах большой мощности. Поэтому к качеству металла труб следует относиться очень требовательно. К сожалению, нередки случаи, когда на котлостроительных заводах или, что еще хуже в процессе эксплуатации выявляются дефекты труб металлургического характера. В связи с этим на всех крупных котельных заводах имеются цехи входного контроля труб перед запуском их в производство.
Входной контроль начинается с внешнего осмотра труб снаружи и изнутри. Трубы визуально контролируются по наружной поверхности с целью обнаружения глубоких рисок, вмятин, трещин, закатов, расслоения и тому подобного. Осмотру подвергается каждая труба по всей поверхности, изнутри трубы диаметром более 70мм осматриваются перископом.
К операциям подготовки труб следует также отнести такие операции, как очистка труб от ржавчины и сортировка.
Достаточно часто на котельные заводы поступают трубы, имеющие значительную коррозию снаружи и изнутри. Для нормального хода дальнейшего производства трубы необходимо очистить от ржавчины. Коррозия снаружи и изнутри может быть удалена химическим путем (промывка кислотой). Однако такой способ удаления ржавчины требует организации сложного травильного хозяйства с кислотными и щелочными ваннами, промывкой труб и т.д., поэтому на котельных заводах этот метод не нашел своего применения.
Наружная ржавчина удаляется с труб на специальных станках, представляющих собой пару круглых вращающихся металлических щеток и рольганг для подачи труб. Снятая ржавчина отсасывается в приемник пыли. Иногда такой станок дополнительно оборудуется газопламенной горелкой, которая устанавливается до щеток. При нагреве трубы часть ржавчины отлетает, т.к. чистый металл и ржавчина имеют разные коэффициенты линейного расширения. Окончательная очистка трубы осуществляется металлическими щетками.
Наружная окалина хорошо может быть удалена пескоструйной обработкой труб, поэтому этот метод очистки труб от ржавчины находит все большее применение в различных установках.
Имеются установки, производящие очистку наружной поверхности труб с помощью иглофрез. Впервые такая установка появилась на ЗИО, далее на БиКЗ, БКЗ и других.Труднее удалить внутреннюю ржавчину из труб. Для этой цели на некоторых заводах применяют ворошители. При ворошении часть ржавчины внутри трубы опадает, и она удаляется путем продувки труб сжатым воздухом. Пыль улавливается в приемник пыли. Конечно, этот метод далеко не совершенен, но он без помех позволяет вести изготовление трубных элементов. Следует иметь ввиду, что перед эксплуатацией трубные поверхности проходят на электростанции кислотную промывку для очистки внутренних полостей поверхностей нагрева котла.
Если трубы после очистки от ржавчины по каким-либо причинам не могут быть запущены в производство, то необходимо произвести пассивацию очищенных поверхностей для предотвращения коррозии.
В последнее время часть труб с трубопрокатных заводов поступает с защитной консервацией. Для возможности выполнения последующих технологических операций требуется удалить эту консервацию. В зависимости от состава защитной смазки она удаляется или теплой водой, или уайт-спиритом, если в ее составе присутствуют масла. Такая промывка труб производится вручную. Удаление консервации может быть осуществлено путем обжига труб в печи или газовыми горелками.
Следующей операцией подготовки труб является сортировка труб по длине, диаметру и толщине стенки. Для рационального раскроя труб необходима их сортировка по длине, так как при поставке труб всегда имеется определенный процент немерных труб. Около 5% труб в партии отличаются по длине на 150-200 мм. Это дает возможность экономичного подбора труб согласно данным раскроя, так как отходы при резке в размер оказываются минимальными.
На котлостроительных заводах сортировку труб осуществляют на механизированных линиях, на которых сортировка по длинам осуществляется автоматически.
Внутри каждой партии целесообразна сортировка труб по фактическим толщинам стенок. Затраты на эту трудоемкую операцию окупаются повышением качества сварного соединения. Простейший способ сортировки такого рода основан на замерах труб контрольными калибрами.
После проведения всех подготовительных операций технолог цеха делает раскрой змеевика или трубы, т.е. определяет расположение сварных стыков на детали и в соответствии с этим количество и конфигурацию отдельных деталей, из которых в дальнейшем будет сварен змеевик или труба.
При составлении раскроя должны учитываться следующие требования:1. Число сварных стыков должно быть наименьшим, а длина стыкуемых труб по возможности наибольшей. Поэтому желательно получить с трубопрокатных заводов трубы большей длины.2. Запрещается располагать сварные стыки на гибах труб и в местах приварки к ним каких-либо деталей.3. Сварные стыки должны быть доступны для ремонта на электростанциях.4. От начала гиба до стыка должен быть прямой участок не менее 250 мм при контактной сварке и не менее 50 мм (но не менее диаметра трубы) при ручной сварке.5. Раскрой должен обеспечить минимальные отходы труб.6. При разработке процесса раскроя следует стремиться к возможно большему количеству одинаковых деталей (см. рис.).
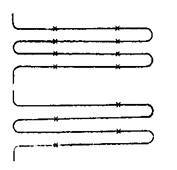
Котельные заводы определяют одно или несколько значений длин труб, которые удовлетворяют перечисленным выше требованиям, и заказывают мерные трубы именно таких длин.
Технолог при определении длины заготовки детали должен иметь ввиду, что трубы при гибке удлиняются.
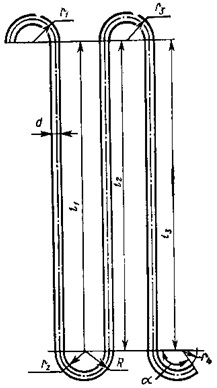
Развертка сложно-изогнутой трубы (змеевика) (см. рис.) подсчитывается по длине нейтральной линии, т.е. по оси трубы. Эта длина для змеевика на рис. Состоит из длин трех прямых участков l1+l2+l3, трех изогнутых на 180° участков и одного неполного, изогнутого на угол α участка. Длина развертки изогнутого участка равна S=(2πrα)/360, (при α=180°, S=πr). Определение развертки входит составной частью в операцию, называемую раскроем труб.
Раскрой производят следующим образом. На миллиметровой бумаге вычерчивают в виде прямой линии всю длину трубного элемента и отмечают на этой схеме положение сварных стыков, границ гибов и приварки деталей. Согласно полученной схеме раскроя определяют соответствующие длины труб и нумеруют заготовки порядковыми номерами. Длину труб назначают с учетом припуска под контактную сварку, т.е. учитывают, что в процессе оплавления труба укоротится. Длины трубных заготовок, подлежащих гибке, назначают с учетом вытяжки, тем самым учитывают, что заготовка в процессе операции гибки удлинится.
Таким образом, длина трубной заготовки отличается от длины трубы в составе трубного элемента на величину допуска под контактную сварку и на величину вытяжки при гибке. Длину трубной заготовки Lз, мм, определяют по следующей формуле:Lз = Lр + δк + δв, где Lр развернутая длина по чертежу, δк – припуск под контактную сварку; δв – величина вытяжки.
За последние годы технология гибки труб усовершенствована настолько, что стало возможным производить их гибку без последующей обрезки концов трубы. Это позволило отказаться от операции резки гнутых труб и перейти на резку только прямых заготовок труб под гибку или контактную сварку.
Существует большое количество труборезных станков.
Оборудование для резки труб можно разделить на две большие группы:1. Станки, при резке на которых обрезаемая труба вращается, а инструмент не имеет вращательного движения.2. Станки, на которых труба при резке не вращается, а инструмент имеет вращательное движение с радиальной подачей.
Оборудование первой группы отличается шумом вращающейся трубы, быстрым износом при резке длинных труб даже с небольшой погнутостью, биением кривой трубы при вращении и связанной с этим опасностью для рабочего и окружающих.
Поэтому, безусловно, предпочтительнее оборудование, на котором труба при резке не вращается. Трудозатраты для второй группы станков на 3-5% меньше.
Обрезанные заготовки поступают на зачистку концов под контактную сварку в целях получения контактной поверхности, свободной от оксидов, механических и жировых загрязнений, обеспечивающей хороший электрический контакт трубы с губками сварочной машины. Длина зачистки зависит от конструкции губок контактно-сварочной машины и обычно составляет 200-250 мм.
Операция зачистки концов труб может быть выполнена несколькими способами:1. Пескоструйной очисткой.2. Зачисткой абразивными камнями.3. Зачисткой иглофрезами.4. Зачисткой непрерывной наждачной лентой.5. Химической зачисткой.
В связи с появлением совершенных контактно-сварочных машин, оборудованных приборами для контроля качества сварки, требования к зачистке концов труб под сварку возросли: кроме зачистки снаружи на длине 250 мм, требуются зачистка внутренней поверхности трубы на длине 15-20 мм, а также зачистка торца трубы. Зачистка внутренней поверхности часто заменяется операцией зенкерования трубы.
Способы изготовления змеевиков и труб поверхностей нагрева
В котлостроении известно несколько различных способов изготовления элементов поверхностей нагрева.
Способ 1. Этот способ был преобладающим в 50-е годы. Предусматривалась резка заготовок труб, гибка всех деталей, зачистка их под сварку, сварка деталей в змеевик или трубу, плазировка, гидравлическое испытание и отделочные операции.

Гибка деталей была одной из первых операций, и все последующие операции (зачистка под сварку, сварка) производились на гнутых деталях.
Плаз представляет собой большую стальную или чугунную плиту, собранную из нескольких прямоугольных частей, соединенных на болтах. При изготовлении серии однотипных змеевиков применяют плазы, на которых вычерченный контур змеевика ограничивается по гибам и в средней части прямых участков вставленными в плаз гладкими штырями и для контроля контура целого змеевика после стыковой сварки.
Способ 2. Повышение параметров пара и применение в связи с этим высоколегированных труб для изготовления пароперегревателей вызвали необходимость разработки другого способа изготовления змеевиков, который первоначально использовался только при из
all4study.ru
Поверхности нагрева котлов - Уральский завод котельного оборудования
Производим поверхности нагрева котлов.
Топочные экраны котла изготавливают из стальных бесшовных цельнотянутых труб.
В котлах с естественной циркуляцией, где движущий напор невелик, экраны выполняют из труб диаметрами 50 и 60 мм с толщиной стенки 4-6 мм.
К радиационным поверхностям нагрева, воспринимающим теплоту от газов в основном за счет излучения, относят экраны, настенные и потолочные пароперегреватели, ширмы, располагаемые в топочной камере.
Ширмовые поверхности нагрева располагают в верхней части топки и соединительном газоходе В зависимости от поперечного. Конструктивно ширмы представляют собой вертикальные U-образные (гораздо реже горизонтальные и L- или W-образные) гладкотрубные или цельносварные ленты с входным и выходным коллекторами, выполненные из труб диаметром 32x5, 32x6, 42x6 мм из стали 12Х1МФ или 12Х18Н12Т.
Ширмы поставляют на монтажную площадку в виде готовых заводских блоков. Вертикальные ширмы крепят на неохлаждаемых тягах к каркасу котла (здания), горизонтальные подвешивают на охлаждаемых подвесных трубах.
Конструкция топочных экранов котла должна обеспечивать надежное охлаждение металла стенки труб, возможное меньшее гидравлическое сопротивление, иметь малую чувствительность к неравномерности распределения тепловосприятия по ширине и высоте экрана, обеспечивать компенсацию температурных расширений труб. Экраны должны быть технологичными, транспортабельными, допускать блочное изготовление, иметь возможно меньшую металлоемкость, быть дренируемыми.
Поверхности нагрева котлов, готовая продукция
В топке котлоагрегатов, размещаются экранные поверхности нагрева, состоящие из стальных труб (или чугунных секций микрокотлов) и воспринимающие тепловое излучение слоя или факела горящего топлива. Высокая эффективность теплообмена обусловливает их небольшие размеры.
Такие экранные поверхности являются основными парогенерирующими элементами современных котлоагрегатов, также защитой стенок топки от воздействия высоких температур и шлакования. Расчетная температура газов на выходе из топки 900-1100 °С.
В газоходах котлоагрегатов размещаются пучки стальных труб. Теплота газов передается им в основном конвекцией, отсюда их название - конвективные. В экранных и конвективных поверхностях нагрева получается насыщенный пар или вода определенной температуры.
ural-zko.ru
Поверхность - нагрев - котельный агрегат
Поверхность - нагрев - котельный агрегат
Cтраница 1
Поверхности нагрева котельных агрегатов, работающие под давлением, можно разделить на три группы: подогревательные ( зкономайзерные), испарительные и перегревательные. [1]
Поверхности нагрева котельного агрегата состоят из радиационной, полурадиационной и конвективной частей. Радиационная поверхность нагрева в топке условно разбита на нижнюю ( НРЧ), среднюю ( СРЧ) и верхнюю ( ВРЧ) части. Боковые экраны имеют перегиб на отметке 11 м и образуют холодную воронку. [2]
Компоновка поверхностей нагрева котельного агрегата должна производиться с учетом конструктивных особенностей передвижной базы. Для устойчивости последней вспомогательные поверхности нагрева ( экономайзера, воздухоподогревателя) выгодно располагать за котлом, а не над ним. [4]
Загрязнение поверхностей нагрева котельных агрегатов, как это было показано в гл. Сопоставление результатов измерения концентрации SO3 после обмывки всех поверхностей нагрева и после длительной эксплуатации без всяких очисток свидетельствует о повышении концентрации серного ангидрида по мере загрязнения поверхностей нагрева. [6]
Для поверхностей нагрева котельных агрегатов применяются только - бесшовные ( катаные или цельнотянутые) трубы, изготовленные из спокойной мартеновской стали. [7]
В поверхностях нагрева котельных агрегатов имеются стыки труб из разнородных сталей - композитные стыки. Подавляющее большинство этих стыков выполняется на заводе. На монтаже сваривают не более 50 - 100 композитных стыков на котел блока 300 Мет. [8]
Наружные загрязнения поверхностей нагрева котельного агрегата снижают теплопередачу гораздо больше, чем отложения накипи на его внутренних поверхностях. [9]
Для изготовления поверхностей нагрева котельного агрегата, работающих при температуре пара до 450 С, широко применяют углеродистую сталь марки 20 с содержанием углерода до 0 25 %, а для изготовления каркаса котлов - углеродистую сталь марки Ст. В низколегированной стали углерод содержится в еще меньшем количестве. [10]
Надежная работа поверхностей нагрева котельного агрегата в значительной степени зависит от качества испаряемой воды. Одной из особенностей процесса испарения воды является выпадение из кипящей воды растворенных в ней различных солей, часть из которых осаждается на поверхностях нагрева в виде плотного слоя с низкой теплопроводностью, называемого накипью. [12]
Необходимо предусматривать очистку поверхностей нагрева котельных агрегатов, работающих на твердом топливе или мазуте. [13]
Образование отложений на поверхностях нагрева котельных агрегатов происходит в результате сложных физико-химических процессов, в которых участвуют не только накипеобразователя, но и окислы металлов и легкорастворимые соединения. Анализ отложений показывает, что наряду с солями накипеобразо-вателей в них содержится значительное количество окислов железа, являющихся продуктами коррозионных процессов. [14]
Образование отложений на поверхностях нагрева котельных агрегатов происходит в результате сложных физико-химических процессов, в которых участвуют не только накипеобразователи, но и окислы металлов и легкорастворимые соединения. Анализ отложений показывает, что наряду с солями накипеобразо-вателей в них содержится значительное количество окислов железа, являющихся продуктами коррозионных процессов. [15]
Страницы: 1 2 3 4
www.ngpedia.ru
Изготовление элементов поверхностей нагрева - Энциклопедия по машиностроению XXL
Документация для изготовления элементов поверхностей нагрева [c.34]Изготовление элементов поверхностей нагрева [c.143]
Контактная стыковая сварка непрерывным оплавлением является основным технологическим процессом при изготовлении элементов поверхностей нагрева котлов. При производстве одного современного котла производительностью 900—1000 т пара в 1 ч этим методом выполняют несколько десятков тысяч стыков труб диаметром 30—50 мм. [c.91]
Для изготовления трубных элементов поверхностей нагрева и коллекторов паровых и водогрейных котлов применяют трубы, поставляемые по ГОСТ 8731—74, ГОСТ 8733—74, ТУ 14-3-460—75 и ТУ 14-3-190—73. Химический состав, механические свойства, а также результаты технологических испытаний и металлографических исследований [c.267]При изготовлении и ремонте трубчатых элементов поверхностей нагрева паровых котлов сварные стыки должны располагаться на прямых участках труб, при этом расстояние от сварного стыка до опоры должно быть не менее 100 мм. [c.969]
Материалы, применяемые для котельных установок. При проектировании котлов и котельно-вспомогательного оборудования одним из важнейших условий обеспечения их надежной работы является правильный выбор металлов и сплавов, особенно для изготовления поверхностей нагрева, подвесной системы, барабанов и коллекторов, узлов креплений и дистанционирования трубных элементов, паропроводов и трубопроводов питательной воды. В котлах все обогреваемые элементы поверхностей нагрева работают под напряжением при высоких температурах металла, что в определенных условиях может вызвать развитие ползучести, коррозии и других процессов, снижающих работоспособность металла из-за снижения его прочности, пластичности и вязкости. При этом чем выше температура металла и напряжение, тем более интенсивно протекают эти процессы. [c.69]
Металлографические исследования стыковых швов трубчатых элементов поверхностей нагрева, трубопроводов в пределах котла и коллекторов (камер) проводятся на образцах, изготовленных из контрольного сварного соединения (табл. 6.11,1). Образцы вырезаются поперек сварного шва и должны включать сечение шва, зоны термического влияния и прилегающие к ним участки основного металла, а также подкладное кольцо, если последнее применялось при сварке и не подлежит удалению. [c.287]
При нарушении технологии изготовления, монтажа и ремонта элементов поверхностей нагрева и недостаточного контроля металла могут появляться технологические трещины, риски и расслоения металла, а также задиры на внутренней поверхности труб. В процессе эксплуатации котлов эти дефекты приводят обычно к образованию продольных разрывов труб. [c.136]
Проверка труб. Трубы для изготовления и ремонта элементов поверхностей нагрева паровых котлов выбирают в соответствии с правилами Госгортехнадзора, ГОСТами и ТУ на поставку, их назначением и температурой рабочей среды. На выбранные трубы должен быть сертификат или данные механических испытаний, технологических проб и химического анализа. [c.125]
Разметка труб под обрезку и гнутье. Поверхности нагрева котлов состоят из прямых и гнутых участков труб, которые свариваются между собой и образуют иногда очень длинный контур для прохода воды или пара. Для изготовления кипятильной или экранной трубы, ширмы, змеевика пользуются чертежом, на котором приведены длины прямых участков, радиусы и углы изгибов и другие данные, определяющие форму и размеры элемента поверхности нагрева. [c.125]
Технические условия на трубные элементы поверхностей нагрева (извлечение из МРТУ 2402-02-65) распространяются на изготовление и поставку следующих элементов стационарных паровых котлов на давление от 40 до 400 кгс/см и температуру среды не выше 650 С [c.171]
На твердой поверхности нагрева центрами парообразования яв-ляются наибольшие углубления и трещинки, заполненные газом или паром. Такие неровности обычно возникают на поверхности в процессе изготовления элементов теплообменников, например труб или плоских стенок. [c.261]
На твердой поверхности нагрева центрами парообразования являются небольшие углубления и треш,ины, заполненные газом или паром. Такие неровности обычно возникают на поверхности в процессе изготовления элементов теплообменников, например труб или плоских стенок. Чем больше центров, тем интенсивнее происходит процесс парообразования. [c.334]
Нагревательные приборы осуществляют непосредственный обогрев помещений. Конструкции их разнообразны. Материалами для изготовления служат чугун, сталь, бетон, керамика и т. д. Основными видами нагревательных приборов являются радиаторы, конвекторы и панельно-лучистые приборы. Нагревательные приборы должны отвечать гигиеническим, эстетическим и технологическим требованиям. Последнее предусматривает возможность получения требуемой поверхности нагрева путем сборки отдельных элементов в один агрегат. [c.374]
Применяемая сейчас при изготовлении поверхностей нагрева котельных элементов контактная стыковая сварка оплавлением [c.142]
При изготовлении поверхностей нагрева на котельных заводах применяют в основном контактную сварку и в меньшей степени — ручную электродуговую. Сварку ответственных элементов, ремонт которых затруднен, производят в среде аргона. В частности, этим способом сваривают трубы поверхностей нагрева паропаровых теплообменников. Аргоно-дуговую сварку применяют для подварки корня шва ремонтных электродуговых стыков поверхностей нагрева котлов мощностью 300 Мет и более с целью обеспечения максимальной надежности, а также на монтаже. [c.167]
Структура металла шва зависит от химического состава. Элементы, повышающие устойчивость аустенита, способствуют получению однофазной аустенитной структуры металла шва, т. е. уменьшению содержания в ней феррита. К этим элементам относятся углерод, никель, марганец, азот, медь и кобальт. Углерод действует очень эффективно, примерно в 10 раз эффективнее никеля. Однако повышение содержания углерода приводит к образованию карбидов и уменьшению коррозионной стойкости металла шва. В аустенитных сталях, применяемых в СССР для изготовления паропроводов и поверхностей нагрева котлов, содержание углерода не превышает 0,12%. В аналогичных сталях ФРГ содержание углерода не превышает а в сталях США —0,08%. [c.180]
Немаловажным показателем эффективности любого теплообменника является его компактность, т. е. объем агрегата (м ), приходящийся на 1 м площади поверхности нагрева или на единицу переданной теплоты в 1 ч. Если для чугунного экономайзера ВТИ она составляет 0,04—0,06, для стального гладкотрубного 0,08—0,085, для регенеративных воздухоподогревателей 0,056 м /м , то для контактных экономайзеров этот показатель с учетом обязательных элементов установки —0,03, а для конденсационных поверхностных теплообменников также около 0,03 м /м (тоже с учетом входной и выходной газовых камер и изготовления этих теплообменников из высокоэффективных труб Костромского калориферного завода). Для других типов труб этот показатель существенно выше. Есть основания полагать, что конденсационные поверхностные и контактные теплообменники по компактности примерно равноценны, за исключением случаев, когда требуется весьма глубокое охлаждение газов до температуры, очень близкой (с разницей 1— [c.250]
Основными материалами для изготовления передвижных паровых котлов служат листовая сталь и стальные бесшовные трубы. Листовую сталь применяют для изготовления элементов, предназначенных для работы под давлением (обечаек, барабанов, днищ, жаровых труб, трубных решеток и др.), и деталей топки, кожуха, дымовой трубы, гарнитуры и т. п., которые не находятся под давлением. Стальные бесшовные трубы применяют для изготовления поверхностей нагрева котельного агрегата (экранов, конвективных пучков, водяных экономайзеров, пароперегревателей), коллекторов, циркуляционных труб и других деталей. [c.243]
Термическая обработка. Ее назначение заключается в снятии внутренних напряжений в металле, возникших в процессе изготовления элементов оборудования (сварке, гибке листов, вальцовке и т. д.). Стойкость сварных соединений аппаратуры из высокопрочных сталей к сероводородному растрескиванию заметно повышается в результате предварительного нагрева листов перед сваркой до температуры 100— 150°С (хотя все же и остается несколько меньшей, чем стойкость основного металла) [132]. Рекомендуется так-нсе [137] применять такую технологию сварки, которая обеспечивает получение сварных соединений с прочностью не более, чем у основного металла [137]. На поверхности швов не должно быть никаких дефектов. В противном случае может иметь место концентрация напряжений и зарождение коррозионных трещин в этих местах. [c.100]
На основе проектной проработки элементов газовоздушного тракта — газовоздухопроводов, поверхностей нагрева парогенератора, внешних газоходов и дымовых труб—при нескольких значениях скорости выбирают вариант с минимальными расчетными затратами. Оптимальная скорость увеличивается с повышением температуры, улучшением аэродинамической формы газохода, уменьшением стоимости электроэнергии и увеличением стоимости материалов, применяемых для изготовления газохода. При этом учитывают ограничение скорости по условиям износа и заноса летучей золой элементов газовоздушного тракта. [c.316]
Использование чугуна ДЛй изготовления элементов поверхности нагрева позволяет значительно уменьшить габариты воздухоподо- [c.47]
Из испытанных материалов удовлетворительная износостойкость лишь у высоколегированных сталей Х18Н9Т и Х28. Однако применять такие стали для изготовления котельных поверхностей нагрева нецелесообразно вследствие их высокой стоимости, склонности к межкристаллитной коррозии при высокой температуре и наличия местного интенсивного износа отдельных элементов котельных поверхностей нагрева при общей удовлетворительной стойкости. [c.118]
Как видно из табл. 2-1 и 2-й, для размещения элементов поверхности нагрева котлоагрегата применяют П- и Т-образную компоновки. В настоящее время при создании газоплотных котлоагре-гатов под наддувом намечается тенденция к применению только И-образной компоновки, которая имеет ряд преимуществ перед Т-образной, в частности по металлоемкости и трудоемкости изготовления и монтажа котлоагрегата. [c.49]
При расположении элементов котлоагрегата, изготовленных из углеродистых сталей, в зоне температур выше 600°С и недостаточном их охлаждении может происходить интенсивное окалинообразование. Ока-линообразование же на деталях котлоагрегатов сопровождается деформацией, что приводит к нарушению плотности и прочности соединений (дверц, опор, прокладок и подвесок в газоходах) и ухудшает работу поверхностей нагрева. Надежная работа углеродистых сталей будет обеспечена в том случае, если температура металла не превышает 500— 600°С, для легированных сталей она может быть повышена до 600- [c.164]
По мере продвижения дымовых газов по газовому тракту температура их снижается и разность между их температурой и температурой среды, воспринимаюш,ей тепло (вода,.пар, воздух), уменьшается. Следовательно, чем дальше от топки по ходу газов расположен тот или иной элемент котельного агрегата, тем менее эффективно используется его поверхность нагрева и, следовательно, тем она должна быть больше, чтобы воспринять заданное количество тепла и тем больше должен быть расход металла для изготовления этого элемента. [c.309]
Для изготовления стоек, дистанционирующих элементов и различных деталей крепления поверхностей нагрева, работающих при высокой температуре в среде дымовых газов, широко используется сталь марки Х23Н18. Однако она подвергается интенсивной коррозии в продуктах сгорания мазутов. Так, стойки конвективных пароперегревателей, изготовленные из этой стали, разрушаются за 5—6 мес при температуре газов около 800 °С. Глубина коррозии стали в таких условиях составляет 7—8 мм за 10 ч. Данные по коррозионной стойкости в продуктах сгорания мазута сталей и сплавов, пригодных для изготовления различных конструктивных элементов топочного пространства, приведены на рис. 13.3 [61. Эти данные, а также результаты промышленного опробования [c.237]
В 1947 г. ТКЗ приступил к изготовлению барабанных котлов высокого давления производительностью 23(1 /п/час, давлением пара ЮОкг/сж и температурой 510° С (фиг. 16) по несколько изменённому проекту котла КО-УП, разработанному в 1944 г. ко.тель-нс-конструкторским бюро ЛМЗ. Котлоагрегат типа ТП-230 может быть отнесён к группе унифицированных котлов, конструкция которых при сжигании различных по своему качеству топлив отличается лишь сравнительно незначительным изменением расмсров поверхности нагрева пароперегревателя и водяного экономайзера, в то время как все прочие элементы котла остаются без изменения. Характерной особенностью этого котла является применение предвключённого барабана небольшого диаметра, в который включены пароотводящие трубы всех экранов. Пари вода после разделения поступают по специальным трубам в нижний, основной барабан, после которого пар, окончательно освободившись от влаги, посту- [c.46]
Экранные поверхности нагрева конструктивно увязывают с элементами тоночных устройств — амбразурами горелок, решетками, гарнитурой и т. н. Для упрощения и ускорения поточного изготовления труб на котлостроительных заводах, их монтажа и ремонта, конфигурация труб в топочной камере должна быть по возможности плавной с гибами одного радиуса. На экранных трубах, огибающих амбразуру горелки, не следует выполнять дополнительных гибов для обвода гляделок, лазов и т. п. [c.70]
Следует отметить, что создание специальных комбинированных пароводогрейных котлов, полностью отвечающих всем поставленным выше требованиям и техническим условиям, является задачей вполне технически разрешимой и выполнимой для наших котлостроительных заводов. Однако при широком серийном производстве крупных прямоточных стальных водогрейных котлов для камерного сжигания газа, мазута и твердого топлива как в слое, так в камерных топках наиболее перспективными для изготовления и широкого выпуска являются комбинированные пароводогрейные котлы, выполняемые на базе стальных прямоточных водогрейных котлов с применением максимальной унификации с ними, т. е. с использованием основных серийно из1Г0Т0вляемых элементов и поверхностей нагрева этих водогрейных котлов. [c.99]
Влияние повышенной температуры на износ изучалось на сталях, используемых для изготовления труб котельных поверхностей нагрева — 20К, 15Х1М1Ф и Х18Н9Т, а также применяемых для изготовления элементов технологического оборудования Ст. 3, Х28. Кроме того, для выяснения возможности использования в теплоэнергетике титановых [c.101]
Столь высокий подогрев воздуха может быть осуществлен только при надежном обеспечении работы котла с ничтожными присосами воздуха в газоходы. В котле 950 т/ч ЗиО даже при весьма низких расчетных присосах воздуха (на всем пути газов от топки до дымососа всего 0,04 от теоретически необходимого воздуха) на горячем конце воздухоподогревателя температурный напор составил 123° С, а поверхность нагрева регенеративного воздухоподогревателя (при 0ух=130°с и /г.в = 300° С) около 100 тыс. м . Поэтому очень важно, чтобы длительно устойчивые бесприсосные качества газоходов были обеспечены тщательными конструктивными разработками и аккуратным изготовлением соответствующих элементов котлов на заводах. [c.96]
В эксплуатации находятся элементы первичных и iBTO-ричных пароперегревателей, изготовленные из стали ЭИ-756, мартенсито-ферритного класса, отличающейся высоким содержанием хрома. Эти трубы выпускались пока небольшими партиями, стоимость их высока, и в работе находится ограниченное количество элементов, изготовленных из этих труб. Однако опыт их работы показал, что при изготовлении труб в соответствии с техническими условиями пароперегревательные поверхности нагрева из них могут работать достаточно надежно. 114 [c.114]
В табл. 7-5 приведены величины изменения поверхностей нагрева, а в табл. 7-6 — изменения капитальных затрат на этн поверхности, а также на паропроводы, регулирующие и пускосбросные устройства в вариантах 2, 3 и 4 по сравнению с вариантом 1 (котел ПК-41) с учетом затрат на изготовление и монтаж. Затраты на изготовление поверхностей нагрева и паропроводов приняты в размере 28% от стоимости материалов затраты на монтаж этих элементов — в размере 20% от стоимости материалов и изготовления. Затраты на изготовление и монтаж рециркуляционной установки приняты по смете СКВ ВТИ. [c.292]
Отклонение от круглоГ формы сечения труб поверхностей нагрева и трубопроводов в гнутых участках, характеризуемое величиной овальности а , не должно превышать значений, указанных в ТУ на изготовление элементов, работающих под давлением. [c.24]
Назначение. Сталь предназначена для изготовления неохлаждаемых элементов днстанционирования и крепления труб поверхностей нагрева пароперегревателей мощных тепловых электростанций, для насадок горелок топочного оборудования, форсунок печного оборудования, деталей различного теплообменного, нагревательного и другого высокотемпературного оборудования, работающего на воздухе и в агрессивных средах продуктов сгорания серосодержащих углей и природного газа при температурах до 1200°С. [c.352]
Газогенератор выполнен в едином корпусе с газоохладителем (рис. 1-2) в виде футерованного огнеупорами вертикального сосуда с установленными пневмомеханическими форсунками. На распыление мазута поступает воздух, необходимый для процесса газификации. Температура в пламени при газификации (окислительная зона) достигает 1700— 1800 С, в восстановительной зоне она снижается до 1300 С. азоохладитель состоит из элементов типа труба в трубе. По внутреннему каналу движется газ, по наружному кольцу — питательная вода. Такая конструкция позволяет снизить отложения и повысить эффективность работы поверхности нагрева газоохладителя. Для подачи воздуха на газификацию и создания избыточного давления в системе установлен специально запроектированный и изготовленный Уральским турбомоторным заводом (ТМЗ) турбонаддувной агрегат. [c.15]
Основные материалы оборудования парогенераторов стали перлитного класса. Широко используются стали (табл. 30.3) с малыми добавками ванадия. В сталях, предназначенных для изготовления труб пароперегревателей, рекомендуется никель заменять элементами с высокой температурой плавления сульфидов и сульфидных эвтек-тик, например марганцем. Аустенитная сталь ДИ-59, содержащая марганец, медь и ниобий, обладает стойкостью в продуктах сгорания высокосернистого мазута при температуре 650 и устойчива к межкрнсталлитной коррозии. Для изготовления шипов и подвесок используют малопластичные, но весьма коррозионно-стойкие сплавы системы Fe—Сг—Si (сильхромы) и Ре—Сг—Si— А1 (сихромали) [3]. При повышении концентрации алюминия и хрома возрастает стойкость к ванадиевой коррозии, добавки молибдена ухудшают стойкость сталей в продуктах сгорания мазута. Для изготовления стоек и подвесок труб газоходов, температура которых превышает температуру поверхностей нагрева, используют хромоникеле- [c.204]
mash-xxl.info
Подготовка к монтажу поверхностей нагрева котла
Категория: Монтаж котлов
Подготовка к монтажу поверхностей нагрева котла
Трубы экранов и конвективного пучка поставляют на монтаж готовыми, не требующими гнутья; в некоторых случаях они состоят из двух-трех частей. Концы труб закрывают металлическими или пластмассовыми колпачками (заглушками).
Барабаны котлов поступают на монтаж с собранными сепа-рационными устройствами и запломбированными люками. Сепа-рационные устройства закрепляют на прихватке, так как на монтаже их приходится вынимать из барабана котла. Трубные отверстия и штуцера покрыты противокоррозионной краской и закрыты металлическими или пластмассовыми колпачками, а фланцы — деревянными, пластмассовыми или металлическими крышками.
Змеевики пароперегревателя и экономайзера поступают на монтажную площадку объединенными в пакеты. Стальной трубчатый воздухоподогреватель поставляют в виде секций, состоящих из вертикальных труб, которые объединены тремя трубными досками. Из них верхняя и нижняя доски скрепляют трубы в секцию, а средняя служит направляющей перегородкой. Секции должны быть испытаны на плотность, а трубные отверстия закрыты заглушками.
Каркас воздухоподогревателя — рама и щиты металлической обшивки — поставляют крупными элементами, размеры которых находятся в пределах железнодорожных габаритов. Регуляторы перегрева пара поступают в собранном виде.
При приемке оборудования и элементов котла проверяют комплектность деталей поверхностей нагрева по отправочным ведомостям или спецификациям рабочих чертежей и маркировке деталей.
Заводы-изготовители прикладывают сертификаты, в которых указывают данные о металле (номер плавки стали, ее марку и химический состав в процентах) и показатели механических испытаний. Номер сертификата выбивают на деталях, и он вместе с другими обозначениями служит маркировкой. Маркировку на трубах поверхностей нагрева наносят на бирку, которую прикрепляют проволокой к связке труб.
На все трубопроводы и другие элементы котла, изготовленные из легированных сталей, завод-изготовитель должен представлять результаты стилоскопирования, которое основано на методе спектрального анализа. Независимо от наличия сертификата элементы котла, работающие при температуре среды 450 °С и выше, подвергают спектральному анализу с помощью стилоскопа для определения наличия легирующих элементов.
В том случае если какие-нибудь детали поверхностей нагрева не имеют маркировки и сертификата, использовать их можно только после проведения химического анализа, а в некоторых случаях — механических испытаний.
При проверке комплектности все элементы поверхностей нагрева осматривают и подбирают по позициям, с тем чтобы при монтаже их легко было найти. При наружном осмотре проверяют отсутствие трещин, вмятин, разрывов, глубоких рисок, закатов, Раковин, чрезмерной коррозии и других дефектов, а также проверяют качество сварных стыков. Обнаруженные дефекты устраняют. Для этого раковины, риски и другие мелкие дефекты выругают или опиливают до полного их удаления, а затем проверяют, “агревая этот участок. Если нагретая поверхность будет одинакового цвета, значит дефект исправлен полностью.
Подготовка труб и змеевиков. При опиливании для устране-Ния наружных дефектов толщина стенок может быть уменьшена Для труб диаметром до 50 мм не более чем на 10 %, а для труб олее 50 мм — не более чем на 0,5 мм. Если же толщина стенки РУбы при опиливании будет уменьшена больше, чем допускаемая величина, то это место вырезают и заменяют вставкой из трубы тех же размеров и той же марки стали. Вставки можно делать только на прямых участках трубы. Расстояние от сварного шва до начала закругления трубы должно быть не менее 50 мм для труб поверхностей нагрева и 100 мм—для трубопроводов в пределах котла.
Часто встречающийся дефект — неточность гибов. Отклонение от номинальных диаметров труб при гнутье регламентируется допуском на овальность, т.е. разностью максимального Dmах и минимального Dmin наружных диаметров, измеряемых в одном сечении.
При подготовке труб поверхностей нагрева к сборке и монтажу проверяют их геометрические размеры. Обязательной проверке подвергают трубы, подлежащие заводке в барабан для вальцевания или приварки к штуцерам барабана, все водоопуск-ные, пароотводящие, соединительные и подвесные трубы.
Если шар не проходит, то зауженное место трубы вырезают и вставляют другой стороной трубы. Экраны, пароперегреватели и водяные экономайзеры проверяют шаром в процессе сборки блока или после их монтажа до гидравлического испытания.
Рис. 1. Определение овальности труб
На плазе размечают по чертежу расположение сечений барабанов, камер и осей труб и змеевиков, соединяющих их. Конфигурацию труб вычерчивают на плазе с отклонениями не более 1 мм от размеров, указанных на заводском чертеже. Трубы, изогнутые в двух и более плоскостях, должны быть вычерчены на плазе для каждой из плоскостей.
Вдоль оси трубы и по торцам на плазе закрепляют фиксирующие планки.
Если конфигурация трубы проектная, то она свободно без подгонки ляжет между планками. В противном случае трубу подгибают, нагревая горелкой. При плазировке можно нагревать трубы, изготовленные из углеродистых сталей (сталь 10, 20). Исправление нагревом гибов труб из легированных сталей (марок 15М, 16М, 15ХМ и 12ХМ) —более сложная операция, так как после нагрева требуется специальная термообработка для нормализации структуры металла труб. Поэтому для исправления таких труб (змеевики пароперегревателей и др.) применяют холодное гнутье, которое выполняют на переносных трубоги-бочных станках.
При плазировке проверяют размер угла загиба и смещения осевой линии. Отклонение отдельных участков трубы от проектного положения не должно превышать 4 мм на 1 м длины участка и не более 6 мм на всю длину трубы. Если труба состоит из двух частей или более, на плазе выверяют все части.
При проверке труб и подготовке их к сборке важная операция — обработка концов труб под сварку. Трубы, состоящие из двух частей и более, поступают с монтажными припусками на концах, которые обрезают механическим способом или газовым резаком с последующей механической обработкой торцов. Концы стыкуемых труб поверхностей нагрева обрабатывают для сварки, снимая с них фаски под углом (30 ±5)° и притупляя кромки на (1 ±5) мм.
Перекос плоскости торца трубы относительно ее оси не должен превышать 0,5 мм. Разность наружных диаметров свариваемых труб должна быть не более 1,5%, а разность толщин стенок труб — не более 15%. Перед сваркой концы труб зачищают до металлического блеска на станках или шлифовальными машинами.
Подготовка барабанов и камер. Поступающие на площадку барабаны и камеры разгружают таким образом, чтобы их можно должен быть не более 1 мм, а смещение кромок —не более 0,5 мм.
Рис. 2. Проверка трубы на плазе: 1 — плаз, 2 — труба, 3 — планки
В том случае, если экранные трубы состоят из двух частей, а в блок входит только одна нижняя камера, трубы до установки в блок выкладывают на плазе и, обрезав монтажные припуски, состыковывают в центровочном приспособлении. После этого трубы раскладывают на козлах и подгоняют к камере. При раскладке на козлах тщательно контролируют шаг трубы с тем, чтобы свободные концы труб блока при монтаже правильно подошли к барабану. С этой целью свободные концы труб зажимают двумя швеллерами. На одном из швеллеров приваривают гребенку, фиксируют шаг труб. После проверки собранного блока трубы приваривают к камере окончательно.
Если натрубную обмуровку устанавливают непосредственно на блок, то гидравлическое испытание собранного блока экрана выполняют до его обмуровки.
При сборке блока следят за тем, чтобы правильно были подобраны позиции труб и чтобы отверстия для гляделок, лазов, горелок были на своих местах. После сборки труб экрана на блоке устанавливают все элементы промежуточных опор и креплений труб блока, детали крепления обмуровки и другие элементы, с тем чтобы не производить этих работ на высоте.
Проходимость труб в собранном блоке проверяют металлическим шаром. Если проходимость труб проверяют на сборочной площадке, то шар продувают через них сжатым воздухом.
Монтаж котлов - Подготовка к монтажу поверхностей нагрева котлаgardenweb.ru
Производство поверхностей нагрева
Продукция: газоплотные панели, блоки пароперегревателей (конвективных, ширмовых, радиационных, потолочных) поверхностей нагрева, водяные экономайзеры, блоки модулей котлов-утилизаторов (КУ).
Технологическое оснащение
- В производстве используются поточно-механизированные линии и установки фирм VKW, DEUMA для сварки под флюсом элементов газоплотных панелей методом «оребрения полосой» или методом «вварки полосы» шириной до 1500 мм длиной до 27 м, после чего элементы укрупняются в панель шириной до 3 метров на портальных сварочных установках.
- Производство оснащено уникальной поточно-механизированной линией по производству мембранных водяных экономайзеров, в которой осуществляется продольное оребрение труб токами высокой частоты на установке «МЕКОПОН».
- Гибка панелей производится на специальных горизонтальном и вертикальном станах, обеспечивающих право- и левостороннюю гибку панелей шириной до 3 м.
- В наличии оборудование для изготовления конвективных поверхностей нагрева, позволяющее изгибать трубы наружным диаметром от 25 мм до 60 мм с относительным радиусом гиба Rгиб./ D тр. > 1.
- Собственное производство коллекторов для поверхностей нагрева оснащено оборудованием для механической обработки, в том числе с ЧПУ. Изготовление коллекторов полностью оснащено необходимым оборудованием для сварки.
Технологические параметры специализированного участка для производства блоков модулей котлов-утилизаторов
- Общая производственная площадь – 15 000 м²;
- Три производственные линии спирального оребрения (HAN-SUNG) труб Ø 25-114 мм и L=22 м производительностью 65 000 шт/год или 7 000 тонн/год;
- Максимальные размеры модуля – 3500х3500х26000 мм;
- Максимальный вес модуля – 160 тонн;
- Производительность участка по изготовлению модулей КУ составляет – 1,8 ГВт или 12 000 тонн;
- Концепция производства – замкнутый цикл, начиная от производства оребрённых труб до отгрузки готовых модулей КУ в рамках одной производственной площадки;
- Производственный цикл изготовления КУ:
- Вертикального типа мощностью до 300 МВт – 6 месяцев;
- Горизонтального типа мощностью до 350 МВт – 4 месяца.
www.tkz.su
Поверхности нагрева котлов, монтаж - Энциклопедия по машиностроению XXL
На ремонтные заварки техническую документацию оформляют так же, что и в процессе монтажа трубопроводов и труб поверхностей нагрева котлов с дополнительным оформлением акта на переварку дефектного стыка. [c.407]При изготовлении поверхностей нагрева на котельных заводах применяют в основном контактную сварку и в меньшей степени — ручную электродуговую. Сварку ответственных элементов, ремонт которых затруднен, производят в среде аргона. В частности, этим способом сваривают трубы поверхностей нагрева паропаровых теплообменников. Аргоно-дуговую сварку применяют для подварки корня шва ремонтных электродуговых стыков поверхностей нагрева котлов мощностью 300 Мет и более с целью обеспечения максимальной надежности, а также на монтаже. [c.167]
Монтаж стальных трубчатых котлов НР-17 и НР-18. Стальные трубчатые котлы НР-17 и НР-18 применяются для водяных систем отопления с температурой воды до 115° и для паровых систем с давлением пара до 0,7 ати. Котлы НР-18 изготовляют в виде правых и левых пакетов. В зависимости от длины пакетов изменяется поверхность нагрева котлов. Пакеты котла сваривают из отдельных секций. Каждая секция состоит из трех вертикальных труб диаметром 82,5/89 мм и высотой 1 300 мм. Вертикальные трубы вваривают внизу и вверху в горизонтальные трубы того же диаметра. [c.55]Все трубы, поступающие для монтажа поверхностей нагрева котлов, должны иметь хорошо отожженные концы, необходимые для их развальцовки и бортовки. [c.95]
При монтаже и ремонте паровых котлов электродуговая и газовая сварка труб поверхностей нагрева котлов, экранов, пароперегревателей и экономайзеров, а также трубопроводов в пределах котла в зимних условиях может производиться согласно следующему [c.969]
МОНТАЖ ЭЛЕМЕНТОВ ПОВЕРХНОСТЕЙ НАГРЕВА КОТЛОВ [c.56]
Кроме формуляров на монтаж отдельных узлов или актов на поузловую сдачу-приемку этих узлов, в процессе монтажа поверхности нагрева котлов в обязательном порядке должна составляться следующая техническая документация [c.125]
Предназначено руководство для слесарей-монтажников, занимающихся монтажем поверхностей нагрева котлов на электростанциях. [c.2]
В процессе монтажа поверхности нагрева котла неожиданно обнаруживается, что в барабане котла отсутствует одно трубное отверстие (очко), которое завод пропустил и не просверлил, а барабан котла перед монтажем не был осмотрен и проверен. Вся работа по набору труб остановилась. Для сверления отверстия в барабане необходима специальная резцовая головка, которой может не оказаться под руками и тогда перерыв в работе окажется весьма значительным. [c.79]
МОНТАЖ ПОВЕРХНОСТИ НАГРЕВА КОТЛОВ 8-1. МЕТОДЫ МОНТАЖА [c.134]
ОСОБЕННОСТИ МОНТАЖА ПОВЕРХНОСТИ НАГРЕВА КОТЛОВ ВЫСОКОГО ДАВЛЕНИЯ [c.174]
Естественно, что говорить об этом периоде как о периоде накапливания опыта по монтажным работам не приходится. Благодаря незначительным весам отдельных элементов оборудования и незначительному объему монтажных работ, а также отсутствию специализированной монтажной организации монтаж велся в большинстве случаев ручным способом — при помощи простейшего такелажа и инструмента. По существу монтаж котельного оборудования в этот период доверялся от начала до конца монтерам. Инженерно-технический персонал завода от монтажа был оторван, а завод в целом освоением монтажа не интересовался. В подобных условиях монтажные функции завода заканчивались сдачей поверхностей нагрева котла под гидравлическим испытанием, ибо в обмуровке котельного агрегата, предшествовавшей его пуску в работу, завод не участвовал. [c.5]
ГЛАВА СЕДЬМАЯ МОНТАЖ ПОВЕРХНОСТЕЙ НАГРЕВА КОТЛА [c.176]
Гидравлическое испытание поверхностей нагрева котло-агрегата в основном имеет назначением проверку плотности соединений. Таким образом, гидравлическое испытание в конечном итоге служит показателем качества монтажа поверхностей нагрева. [c.259]
В практике эксплуатации паровых котлов наиболее часто наблюдается появление кислородной коррозии. Кислород является одним из главных коррозионных агентов. Начальная стадия кислородной коррозии поверхности нагрева котла возникает при его изготовлении и в процессе монтажа. [c.98]
Надо отметить, что в Руководящих указаниях по ремонту поверхностей нагрева котлоагрегатов (Госэнергоиздат, 1946) и в Инструкции по ремонту поверхностей нагрева паровых котлов (Госэнергоиздат, 1953) указаны несколько меньшие допуски на отклонения по шагу и из ряда (-)- 3 и 5 мм), но практически для условий ремонта более приемлемыми являются допуски + 5 и + 10 мм, принятые в Руководящих указаниях по монтажу поверхностей нагрева котлов" (Госэнергоиздат, 1946). [c.129]
Трубы поверхностей нагрева котлов контролируют при каждом ремонте и гидравлическом испытании путем визуального осмотра с целью выявления труб, имеющих большую остаточную деформацию, коррозию, эоловой износ, трещины в сварных соединениях, недопустимую овальность и другие дефекты [27]. Трубы поверхностей нагрева котлов, изготавливаемые по проекту из легированных сталей, контролируют перед монтажом (или перед установкой во время ремонта) в соответствии с [8]. [c.344]
В последнее время аргоно-дуговая ручная сварка получила широкое распространение во многих отраслях народного хозяйства. На монтаже электростанций этот метод с успехом применяется при сварке монтажных стыков труб поверхностей нагрева котлов из различных сталей. [c.195]
Ручную дуговую сварку покрытыми электродами широко используют при монтаже котлов п паропроводов, а в заводских условиях — при изготовлении тройников, сварке блоков трубопроводов п приварке труб поверхностей нагрева к коллекторам, а также при сварке литых деталей турбин п заварке дефектов литья. Автоматическую сварку под слоем флюса применяют при сварке паропроводов и приварке донышек к коллекторам в заводских условиях. Полуавтоматическая сварка в среде углекислого газа начала использоваться при монтаже паропроводов. Аргоно-дуговая сварка вольфрамовым электродом применяется как в заводских, так и в монтажных условиях при сварке корневых слоев кольцевых швов труб поверхностей нагрева котлов и паропроводов, когда сварка осуществляется без подкладных колец. [c.87]
Монтаж поверхности нагрева котла 245 [c.245]
МОНТАЖ ПОВЕРХНОСТИ НАГРЕВА КОТЛА [c.245]
Монтаж поверхности нагрева котла выполняется в следующем порядке. [c.245]
Установка барабана и выверка его на опорах — важные монтажные операции, выполняются они особо тщательно. От точности выверки барабана зависит качество всего монтажа поверхностей нагрева котла. [c.246]
Монтаж поверхности нагрева котла 247 [c.247]
Монтаж поверхности нагрева котла 249 [c.249]
Во второй половине 80-х годов В, Г. Шухов руководил в конторе Бари монтажом и наладкой водотрубных котлов зарубежных фирм. Его неприятие тяжелых, неуклюжих форм, постоянное стремление делать конструкции лаконичнее, технологичнее, удобнее в эксплуатации проявились и в области котлостроения. Инженер предложил свой вариант горизонтального котла (рис. 234), в котором расположил пучки труб, набранных в шахматном порядке, под углом к горизонту большое число люков для прочистки заменил двумя люками увеличенного диаметра предусмотрел изменение поверхности нагрева за счет длины труб или параллельной установки дополнительных барабанов с одинаковыми по длине трубами. В результате уже с [c.118]
Станок предназначен главным образом для обрезки концов труб, из (Которых сделана поверхность нагревй котла экранных, кипятильных, эко1номайзерны1х, пароперегревательных и других. Эту обрезку приходится выполнять в тех случаях, когда котлостроителыный завод присылает трубы с припусками для окончательной подгонки их длины на монтаже. [c.220]
Отжиг концов труб. Как правило, трубы для поверхностей нагрева котлов долж Ны прибывать на монтаж в отожженном сосгоянии, о чем должно быть указано в сертификате завода-изготовителя. [c.207]
Другим видом ручной сварки, применяемой на монтаже, является ацетилено-кислородная сварка. Она распространена при выполнении монтажных стыков труб поверхностей нагрева котлов, дренажных линий, байпасов и трубопроводов при диаметре труб менее 100 мм. Газовая сварка также отличается очень большой маневренностью, что позволяет применять ее в самых труднодоступных местах, там, где другие способы неприменимы. Вместе с тем по качеству сварных соединений газовая сварка значительно уступает электродуговой и газоэлектрической сварке и поэтому в последнее время она находит все более и более ограниченное применение. [c.9]
Термическая обработка стыков трубопроводов. Термическая обработка всего трубопровода или целых узлов поверхностей нагрева котлов в условиях монтажа практически невозможна. Поэтому в монтажной практике применяется местная термическая обработка сварных соединений, прн которой в зависнмо-214 [c.214]
Монтаж водогрейного котла ПТВМ-ЗОМ. Поверхности нагрева котла поступают в блочном исполнении. Если грузоподъемность монтажного механизма позволяет, то в состав блоков включают и обмуровку. [c.154]В закрытом здании котельной монтаж котла ПТВМ-ЗОМ ведут краном МКГ-25 (рис. 138). После сборки каркаса котла (см. рис. 120) устанавливают конструкции для опирания экранных блоков. Монтаж блоков поверхностей нагрева котла ПТВМ-ЗОМ выполняют следующим образом. Вначале монтируют топочные блоки, последовательно раскрепляя их между собой и каркасом котла. [c.155]
Поверхности нагрева котла КВ-ГМ-100 поставляются заводо.м блоками (рис. 140), которые перед монтажом укрупняют, что значительно сокращает объем подгоночных и сварочных работ на вы- [c.156]
При монтаже сварка труб поверхностей нагрева котлов, экранов, пароперегревателей и экономайзеров, а также трубопроводов в пределах котла может про 13водиться для элементов из углеродистой стали (с содержанием углерода до 0,2%) при температуре до —20° С, из углеродистой стали с содержанием С = -0,21—0,28% и молибденовой стали (16М) — прп температуре до —10° С, а из хромомолиб-деновой стали (12 МХ, 15 ХМ, 12 МФХ, 12ХМФ)—при температуре до —10° С с подогревом стыка до 250—400° С. Стали аусте-нитиого класса могут свариваться только при ноложительпоп температуре. [c.361]
На основных монтажных работах наиболее целесообразна организация небольпгого количества крупных комплексных бригад, каждая из которых работает п дгк -три смены и охватывает все однородные узлы агрегата (например, металлоконструкции котла, поверхности нагрева котла, узлы собственно турбины и т. п.). Применение специализированных бригад целесообразно при монтаже вращающихся механизмов и насосов. [c.532]
На рис. 65 показана ступень двухпоточного экономайзера котла СКД энергоблока 300 МВт для сжигания экибастузского угля. В отличие от предыдущей конструкции опоры 5 дистан-ционирование труб 4 осуществляется стойками 3, закрепленными (за исключением средних) на входных 2 и выходных 1 коллекторах. Экономайзер разделен на два пакета с монтажным стыком между ними. Вода из экономайзера отводится по обогреваемым водоотводящим трубам, которые являются несущими конструкциями, расположенными внутри газохода. Высоту пакетов (1 — 1,5 м), расстояние между ними (0,8—1 м, иногда 0,8—1,5 м) и соседними поверхностями нагрева выбирают из условий монтажа и ремонта. Большие значения принимают для трубных пучков с малым поперечным шагом. [c.104]
Башенная компоновка (рис. 112, в) наиболее эффективна при сжигании под наддувом газа, мазута и многозольных углей. Отличается удобством обслуживания горелок и минимальными (в плане) размерами котельной ячейки. Скоростные и эоловые поля равномерны по сечению газохода, нет зон с повышенным локальным абразивным износом труб ввиду отсутствия поворота потока продуктов сгорания. К недостаткам следует отнести резкое увеличение высоты котла усложнение монтажа наличие ничем не занятого опускного газохода большой длины и размеров дополнительные статические и динамические нагрузки от тяго-дутьевых машин на каркас котла несколько большую протяженность паро-и водопроводов. Очистка поверхностей нагрева от загрязнений водяная или паровая. Такую компоновку применяют для котлов паропроизводительностью D [c.174]
Обмуровка котлов облегченная, натрубная, каркас упрощенный, так как нагрузка от металлической части котла и цепной решеткп передается непосредственно на фундг мент. Все котлы поставляются заводом-нзготовителем в виде блоков и готовых деталей цепных решеток, собираемых при монтаже. Котлы оборудуются системой дробевой очистки конвективных поверхностей нагрева и системой обдувки радиационных [c.256]
У котла типа ДКВР (рис. 23-1,6) имеются два барабана верхний—-длинный и нижний — короткий. Нижний барабан соединен с задней половиной верхнего барабана системой завальцованных в барабаны и расположенных в коридорном порядке гнутых цельнотянутых стальных кипятильных труб наружным диаметром 51 мм, образующих развитую конвективную поверхность нагрева. Под передней половиной барабана находится топочная камера, боковые стены которой покрыты экранами из гладких труб также диаметром 51 мм. У котлов паропроизводительностью 10 т/ч в топке, кроме того, размещены передний и задний экраны. Топка шамотной стенкой разделяется на две части — собственно топку и камеру догорания. Это удлиняет путь тазов в топке до входа в котельный пучок и улучшает условия догорания уноса. Дымовые газы выходят из топки через особое окно, расположенное в правом углу разделительной стенки, проходят камеру догорания справа налево и с левой стороны котла поступают в котельный пучок, омывая его поперечным горизонтальным потоком. В котлах ДКВР устанавливают вертикальный змеевиковый пароперегреватель, набираемый из стальных цельнотянутых труб наружным диаметром 38 мм. Его размещают в начале котельного пучка, отделяя от камеры догорания двумя рядами котельных труб. Для того чтобы можно было разместить пароперегреватель, часть котельных труб не устанавливают. Котлы компонуют таким образом, что их трубный пучок и экраны в сборе с барабанами, коллекторами и опорной рамой вписываются в железнодорожный габарит это позволяет собирать металлическую часть котла на заводе и доставлять ее на монтажную площадку в собранном виде, что упрощает монтаж котла. [c.287]
mash-xxl.info