- 8 (495) 7487600
- 8 (495) 7487600
- 8 (925) 5552040
- 8 (925) 5552040
- Напишите нам
- Обратный звонок
Интернет магазин оборудования насосной, отопительной и водонагревательной техники №1
Мы промоем ваш котел сульфаминовой кислотой недорого! Кислотная промывка паровых котлов
ВНУТРЕННЯЯ ОЧИСТКА ПОВЕРХНОСТЕЙ КОТЛОВ
Ремонт паровых котлов
Внутренняя очистка поверхностей котлов производится для удаления солей, выпадающих из воды и отлагающихся на стенках барабанов, коллекторов и труб. Выпадение солей происходит • при нагревании и испарении воды, причем в некоторых случаях выпадающие соли равномерно покрывают внутренние стенки котла плотной и трудноотделимой коркой, которая называется накипью. В котлах встречается твердая, вязкая и рыхлая накипь. Наиболее опасной является вязкая накипь, обладающая низкой теплопроводностью. Наличие слоя накипи затрудняет теплопередачу от газов к воде. В некоторых случаях слой накипи толщиной 0,2 мм может вызвать недопустимый перегрев стенок труб и образование выпучип или пережог металла.
На внутренней поверхности экранных труб котлов высокого давления, особенно в зоне максимальных тепловых напряжений, появляются отложения накипи, которые могут привести к появлению свищей и к развитию интенсивной подшламовой коррозии, чаще всего около сварных соединений. Отложения образуются в результате нарушения водного режима. Для устранения накипи питательную воду подвергают химической очистке.
Если по каким-либо причинам в котле появляются отложения накипи, то в период капитального ремонта, а для котлов паропроизводительностью менее 0,7 т/ч — согласно утвержденному графику — производят механическую или химическую очистку внутренней поверхности барабанов, труб и других элементов котла.
Перед механической очисткой барабана необходимо проверить температру внутри него, обеспечить приток воздуха, снять и удалить сепарационное устройство.
Чтобы применить наиболее эффективный способ очистки поверхностей котла, необходимо определить характер накипи, ее толщину и твердость.
После выпуска воды из котла следует удалить еще не успевший сцементироваться рыхлый слой накипи. В процессе очистки интенсивно охлаждают рабочее место в барабанах при помощи специальной переносной вентиляторной установки.
В первую очередь производится очистка внутренних поверхностей стенок барабанов и коллекторов от отложений приспособлениями — накидными головками, приводимыми в действие через гибкие валы от электродвигателя или воздушной турбинки. Головку накладывают на очищаемую поверхность и плавно нажимают на нее. При этом необходимо строго следить, чтобы ось головки была параллельна обрабатываемой поверхности. Головки для очистки накипи подбирают в зависимости от диаметров труб и степени загрязнения. Диаметр головки в сложенном виде должен быть на 3—4 мм меньше свободного от отложений диаметра трубы и в свету. При небольших отложениях очистка труб производится равномерной подачей гибкого вала с головкой вперед, а в случае прочных отложений — возвратно-поступательной подачей. Для предотвращения поломок головок и обрывов гибких валов на броне ставится контрольная отметка трубы, далее которой гибкий вал пропускать не следует.
Очистку труб шарошками во всех случаях необходимо производить с одновременной обмывкой водой места очистки. При этом производится и охлаждение шарошек, и смыв накипи, забивающей пространство между зубьями шарошек. Переставлять головку из одной трубы в другую необходимо только при остановленном электрическом или пневматическом приводе.
При удалении накипи в местах, не доступных для очистки головками (в углах соединений перегородок, около выступающих концов труб и т. д.), применяют ручной инструмент — шаберы, скребки, ерши и т. д.
Не рекомендуется отложения чистить молотками с острыми кромками с обеих сторон (клевачи), так как при этом можно повредить поверхность барабана на 0,5—1,0 мм, что вызовет коррозию металла.
Очищенную ручным или механическим инструментом поверхность обмывают струей воды, после чего проверяют качество очистки.
Наиболее эффективным способом химической очистки котлов является промывка их ингибированным раствором соляной кислоты. Этот способ применим как для чугунных, так и для стальных секционных котлов. Однако кислотная промывка котлов, имеющих дефекты металла в заклепочных, вальцованных и сварных соединениях (неплотности, трещины, поры и т. п.), не допускается.
Количество кислоты, потребное для растворения накипи, зависит от количества накипи в котле. Растворы концентрацией более 6 % и менее 2 % не применяются. На каждый 1 мм накипи концентрация раствора соляной кислоты увеличивается на 1 %. Если средняя толщина накипи более 6 мм, химическая очистка производится в два-три приема. В качестве ингибитора (замедлителя) при очистке применяют технический уротропин, формалин, уникол, столярный клей, ингибиторы ПБ-5 и ПБ-6. Количество замедлителя зависит от концентрации кислоты: для 2—3 %-ной концентрации кислоты— 1,5 г/л уротропина (или ингибитора ПБ-5, ПБ-6) или 2,5 г/л столярного клея; для 4—5 %-ной концентрации кислоты— 2 г/л уротропина (или ингибитора ПБ-6) или 3 г/л клея; для 6 %-ной концентрации кислоты — 2,5 г/л уротропина (или ингибитора ГІБ-5, ПБ-6) или 3,5 г/л клея.
Приготовление раствора соляной кислоты и заполнение котла производятся следующим образом:
А) в заполненный водой растворный бак по расчету подается предварительно ингибированная кислота в количестве, Обеспечивающем заданную концентрацию;
Б) раствор перемешивается с помощью насоса путем создания циркуляции по контуру «растворный бак — насос— растворный бак»;
В) приготовленный раствор подается в котел с помощью насоса через нижние точки;
Г) в освободившемся растворном баке готовится новая порция раствора. Операция повторяется до тех пор, пока котел не будет заполнен раствором полностью, а в растворном баке будет остаток для обеспечения залива насоса.
При проведении химической очистки котла следует пользоваться раствором с температурой 25—30 °С. Для более эффективной отмывки котла желательно обеспечить циркуляцию моющего раствора по контуру «промывочный бак—насос—котел». При отсутствии промывочного насоса для обеспечения циркуляции моющего раствора можно использовать огневой обогрев. При растворении накипи происходит бурное выделение углекислоты и образование пены, которая, заполняя трубы, мешает доступу кислоты к очищаемой поверхности и снижает эффект химической очистки. Для удаления углекислоты погашения пены на котле необходимо открыть воздушники и иметь в схеме промывки открытый бак, расположенный выше здания котельной.
Во время кислотной промывки необходимо соблюдать правила техники безопасности, обеспечить надежную вентиляцию котельной, персонал обеспечить спецодеждой и защитными очками и запретить производство сварочных работ на котле до окончания промывки.
Окончание промывки определяется по прекращению образования пены и стабилизации концентрации кислоты в промывочном растворе. Продолжительность кислотной промывки — 3—5 ч. Отработанный промывочный раствор сливается в специальный бак, затем нейтрализуется известью и сбрасывается в специальные емкости небольшими порциями.
Очищенные поверхности котла после слива кислоты должны быть запассивированы. Для пассивации применяются растворы тринатрийфосфата, каустической или кальцинированной соды 0,5 %-ной концентрации. Котел заполняется щелочным раствором до среднего уровня, после чего осуществляется циркуляция пассивирующего раствора в течение 3—5 ч либо промывочным насосом, либо за счет естественной циркуляции при огневом обогреве топки. После охлаждения щелочной раствор дренируется из котла, а поверхности нагрева остаются за - пассивированными.
Очистку специальных устройств барабанов и съемных внутрибарабанных деталей производят химическим способом. Снятые устройства разбирают и укладывают в ванну, наполненную 5—10 %-ным раствором соляной кислоты. По истечении 15—20 мин уложенные детали вынимают из ванны и промывают сильной струей воды. Иногда перед промывкой водой их очищают металлическими щетками.
Промывка пароперегревателя является единственным способом очистки его змеевиков. Своевременная и правильно проведенная промывка способствует длительной и надежной работе пароперегревателя. В качестве промывочной воды необходимо применять конденсат, который лучше разрыхляет и растворяет соли.
Качество индивидуальной промывки, т. е. чистоту змеевика, контролируют по содержанию солей и шлама в воде, выходящей из него. В том случае, когда промывку ведут химически очищенной водой, по окончании промывки змеевик промывают еще конденсатом, чтобы в нем не осталась промывочная вода, которая при выпаривании дает отложения. Воду из змеевика можно удалить сжатым воздухом с давлением 0,4—0,5 МПа (4— 5 кгс/см2) через плотно вставленный наконечник.
Общая промывка пароперегревателя может производиться в период кратковременной остановки котла на 1—3 сут. Перед общей промывкой предохранительный клапан пароперегревателя регулируют, чтобы он открывался при 25 % нормального рабочего давления. После этого пароперегреватель заполняют химически очищенной водой с температурой 50—70 °С по специальному промывочному трубопроводу 0 38—50 мм. Доступ воды в пароперегреватель и продувку прикрывают, давление поднимают почти до 25 % нормального рабочего и поддерживают его около 2 ч. По истечении указанного промежутка времени открывают продувку, подают воду и промывают пароперегреватель в течение 15—20 мин при давлении 25 % нормального. Операцию промывки повторяют несколько раз и следят за содержанием солен и шлама в промывочной воде.
Котлы Е-1/9-1М, работающие на жидком топливе, оборудуются горелочными устройствами АР-90. Для защиты котла подача топлива автоматически прекращается при понижении уровня воды в котле ниже допустимого, при повышении давления пара в …
При изготовлении, монтаже и ремонте элементов котлов, пароперегревателей и экономайзеров должны применяться только стыковые соединения при сварке обечаек, труб (патрубков) и приварке выпуклых днищ, а также тавровые и угловые или …
А. Баранов
msd.com.ua
Сульфаминовая кислота для промывки оборудования отопления
Наша фирма более 17 лет занимается вопросами химической и гидропневматической очистки отопительного оборудования и приборов. Богатый опыт коллектива специалистов компании и профессиональное оснащение промывочными устройствами и химическими реагентами, позволяет квалифицированно и недорого выполнять очищение теплообменников и систем отопления на должном уровне. Также в свои возможности мы зачисляем применение сульфаминовой кислоты во время промывок отопительных систем и котлов в деликатном режиме профилактики.
В Москве и Московской области высокой популярностью среди владельцев котельного оборудования пользуется техническая услуга по химической промывке загрязненных теплообменников котлов отопления и их оснастки. Промывка теплообменных узлов является удаление вредных веществ, которые образуются на внутренних поверхностях нагревательных устройств, препятствуют их нормальной работе и даже способны вызвать поломки дорогостоящего оборудования вплоть до его замены. Большинство этих веществ, накапливающихся в газовых котлах и бойлерах косвенного нагрева (газовых нагревателей), прекрасно удаляются кислотами. В состав кислотных промывочных растворов могут входить совершенно разные кислоты как органические, так и неорганические.
Сульфаминовую кислоту трудно отнести к чисто неорганической или чисто органической кислоте. Она является органическим производным серной кислоты. Ее называют и аминосульфоновая, и амидосерная кислота. Как и все остальные кислоты, сульфаминовая кислота, прекрасно справляется с растворением вредных отложений внутри котлов и бойлеров. Однако имеет ряд преимуществ. В отличие от большинства неорганических кислот, которые чаще всего применяют при промывке, эта кислота твердая. Следовательно, ее проще транспортировать и хранить. Ее проще дозировать для приготовления промывочных жидкостей. Сульфаминовая кислота применяется в виде раствора с достаточно низкой концентрацией и в таком виде совершенно безвредна для человека. Ко всему прочему, она оказывает более щадящее действие на металлы, из которых изготовлены внутренние компоненты оборудования. Но даже в случае использования сульфаминовой кислоты присутствие в системе ингибиторов обязательно.
Учитывая количество комплектов средства для химпромывки, которые естественно теряют свои свойства при удалении серьёзных загрязнений, и повторное использование специальной очистки не исключается, чтобы довести техсостояние приборов и обвязки котла до максимально качественных возможностей эксплуатации. Цена профилактической работы (допработ) и стоимость реагента для кондиционного завершения чистки могут изменяться. Как правило, спецпромывка производится с одним набором «химии», максимально с двумя. Все нюансы уточните до начала промывочных работ в Вашем загородном доме, тем не менее, вся техническая ситуация с системой и котлом отопления известна выездному мастеру во время диагностики, о чём Вы будете знать до производства работ по промывке.
Заказ на химическую очистку теплообменников и системы отопления и ГВС.
Как оценить промывку котла сейчас.
Накипь в теплообменнике не видна и она причина всех аварий котла.
02.01.2018
02.01.2018
14.09.2017
12.09.2017
08.09.2017
analyzer-w.ru
Технологические режимы очистки
Технологический режим химической очистки выбирается на основании определения состава и количества образовавшихся отложений, удаленных с поверхности вырезанных из котла образцов труб.
Для химических очисток водогрейных котлов в зависимости от состава и количества отложений можно использовать в качестве моющих реагентов соляную и сульфаминовую кислоты, концентрат или конденсат низкомолекулярных кислот (НМК). Характеристики этих и ряда других применяемых при химических очистках реагентов приведены в приложении.
Для удаления отложений, состоящих из карбонатов и окислов железа, при загрязненности более 1500 г/м2 целесообразно применение соляной кислоты с предварительным щелочением растворами едкого натра, кальцинированной соды или их смеси. Количество циклов обработки щелочью и кислотой в этих случаях определяется в лабораторных условиях при очистке образцов с максимальной (из вырезанных образцов) загрязненностью и корректируется в процессе химической очистки по данным химического контроля.
При очистке отложений, содержащих кремний, в щелочной раствор и в раствор соляной кислоты необходимо добавление фтористых солей аммония или натрия.
Для гашения пены, образующейся в процессе очистки соляной кислотой, целесообразно применение пеногасителей, например фракция С5–С6 синтетических жирных кислот.
Последовательность технологических операций при химической очистке определяется в режимной карте.
Для обеспечения полноты удаления отложений в процессе очистки необходимо выдерживать следующие скорости движения растворов реагентов и отмывочной воды: при обработке химическими реагентами и промежуточных водных отмывках – не менее 0,3 м/с, при окончательной водной отмывке – не менее 1,5 м/с.
Обработка растворами щелочи и кислоты производится с циркуляцией их по замкнутому контуру. Отработанные растворы и отмывочная вода после промежуточных водных отмывок направляются в систему обезвреживания промывочных растворов. Отмывочная вода при окончательных водных отмывках направляется в теплосеть после удовлетворительных анализов.
При выполнении всех технологических операций (за исключением окончательной водной отмывки сетевой водой по рабочей схеме) для водных отмывок и приготовления растворов реагентов используется техническая вода, прошедшая механическую очистку на сеточных фильтрах. Ориентировочное количество воды, затрачиваемое на каждую водную отмывку, составляет 10 – 15 объемов котла.
4.8.5. Важнейшие реагенты для удаления отложений из водогрейных и паровых котлов низкого и среднего давлений
1. Соляная кислота техническая и ингибированная.
2. Серная кислота контактная, техническая.
3. Сульфаминовая кислота.
4. Концентрат или конденсат низкомолекулярных органических кислот (HMK).
5. Трилон Б – этилендиаминтетрауксуснокислый натрий (ЭДТ Na2).
6. Фторид натрия или бифторид аммония.
7. Силикат натрия (жидкое стекло или силикат-глыба).
8. Щелочные реагенты: едкий натр, кальцинированная сода, тринатрийфосфат, бикарбонат натрия (двууглекислая сода), аммиак, известь.
9. Нитрит натрия – азотистокислый натрий.
10. Пеногаситель – смесь дикарбоновых кислот C5 – С6.
11. Ингибиторы: уротропин, ПБ-5, тиомочевина, тиосульфат натрия, ОП-7, ОП-10, каптакс, катапин.
Серная кислота может применяться только при отсутствии в котле кальциевых накипей, т. е. содержащих СаСОз.
Для предпускового щелочения водогрейных и паровых котлов с давлением до 4 МПа применяются:
Реагенты для щелочения | Для новых | Для загрязненных |
Едкий натр NaOH твердый 95 – 100 %, кг/м3 | ||
Тринатрийфосфат NaPO4 · 12h3O, кг/м3 | ||
Только для котлов низкого давления | ||
Сода кальцинированная NaCO3, безводная, кг/м3 | 7,5 | |
Серная кислота 94–95-процентная для нейтрализации сбрасываемых щелочных растворов, если они повторно не используются, кг/м3 | 6,5 |
Виды основных моющих растворов и режимы их применения.
1. Соляная кислота техническая – 2–6 % HCl; уротропин – 0,8–1,2 %, дикарбоновые кислоты С5 – С6 – 0,02–0,05 % (только при содержании в отложениях более 10 % СаСО3, температура (60 ± 5) °С; продолжительность 6–8 ч.
Раствор пригоден как для промывки травлением, так и при циркуляционной промывке.
2. Соляная кислота ингибированная – 2–6 % HCl, уротропин – 0,5 %, дикарбоновые кислоты С5 – C6 – 0,02–0,05 %. Все остальные условия те же, что и у раствора 1; применим при наличии в отложениях более 10 % SiO2, в воде 1 % NaF.
3. Сульфаминовая кислота – 2–3 % HSO3Nh3, моющее средство ОП-7 или ОП-10 – 0,1 %, каптакс – 0.02 % температура (95 ± 5) °С, продолжительность 6–7 ч.
4. Низкомолекулярные кислоты (НМК) 7–10 % в пересчете на уксусную кислоту, моющее средство ОП-7 или ОП-10 0,1 %; температура (90 ± 5) °С; продолжительность 6–8 ч. НМК рекомендуется применять в основном для удаления карбонатных отложений из паровых и водогрейных котлов, трубопроводов тепловых сетей и теплообменников с латунными трубками.
5. Растворы для щелочения и нейтрализации
NaOH 2–3 %,
или Na2CO3 3–5 %,
или смесь NaOH + Na2CO3 по 2,5 %,
или аммиак до 1 % или до
рН = 10...10,5.
Все растворы без аммиака можно кипятить.
6. Растворы для пассивации промытой поверхности, особенно при намечаемом простое котлов в резерве: метасиликита натрия Na2SiO3 – 0,5 % при 60–80 °С; нитрита натрия NaNO2 – 1 % с аммиаком – 0,5 % при 50–55 °С; аммиака 0,5 % при 60–80 °C (при простое не более 5 суток).
Контрольные вопросы
1. Условия выделения карбоната кальция.
2. Перечислите процессы образования накипи в водогрейных котлах.
3. В чем заключается оценка интенсивности накипеобразования в водогрейном оборудовании?
4. Основные физико-химические процессы, протекающие в воде котлоагрегатов.
5. Выделения твердой фазы в форме накипи и шлама.
6. Состав, структура и физические свойства отложений в парогенераторах.
7. Условия образования твердой фазы из солевых растворов.
8. Условия образования железоокисных и железофосфатных накипей.
9. Образование отложений на поверхностях конденсаторов.
10. Отложения на проточной части паровых турбин.
11. Образование отложений в водогрейном оборудовании.
12. В чем заключается сущность химических очисток теплоэнергетического оборудования?
13. Цель и задачи предпусковой очистки.
14. Когда производится эксплуатационная очистка?
15. Эксплуатационная очистка паровых турбин.
16. Эксплуатационная химическая очистка водогрейных котлов.
17. Перечислите важнейшие реагенты для удаления отложений в теплоэнергетическом оборудовании.
Глава пятая
Похожие статьи:
poznayka.org
Промывка оборудования кислотами
Используемые в каждом случае реагенты (ортофосфорная, соляная кислота, каустическая сода и т.д) тщательно подбираются в зависимости от материала оборудования - стали (углеродистая, адмиральская), чугуна, латуни, меди, бронзы, хрома или медно-никелевого сплава. Так, например, кислотно-щелочная промывка теплообменника чугунных котлов поможет избавить его от оксидов железа и солей кальция и магния.
Процесс чистки агрегата начинается со слива воды из контура. Затем к оборудованию подключается специальная установка, в которой предусмотрен бак с реагентом. Время циркуляции по котловым трубам кислотного раствора зависит от характера отложений и степени загрязненности, но обычно этот период составляет 4-7 часов. Когда накипь полностью растворится под воздействием реагента, рабочий состав с растворенными в нем отложениями сливается. Затем оборудование промывается проточной водой.
КАУСТИЧЕСКАЯ СОДА
Данная разновидность очищающего средства изготавливается либо в составе гелей, либо в виде гранул и широко применяется в качестве агента для устранения засоров в канализационных или отопительных трубах путем растворения отложений. Засоры дезагрегируются гидроксидом натрия, после чего легко продвигаются далее по трубам.
Обычно промывка котлов каустической содой или солью используется для обезжиривания нового оборудования любых типов. Также подобный вид очистки рекомендуется для устранения вторичной окалины или загрязнений объемом от 5 до 30%. Вышеописанная процедура очень актуальна для применения в промышленной сфере, где необходимо постоянно очищать различные резервуары и ёмкости от нагара или остатков сырья. Так как сложнее всего с внутренних поверхностей теплообменного оборудования удаляется именно жир, то промывка котлов каустиком является наилучшим способом устранения подобных отложений, благодаря такому свойству едкого натра (NaOH), как эффективное разрушение жиров.
Процедура промывки паровых и других типов котлов каустической содой способствует быстрому и качественному удалению с внутренних поверхностей теплообменников кремнекислых, маслянистых и др. загрязнений, а также окалины и отдельных частей рыхлой ржавчины, образованных при производстве, установке или хранении оборудования. Данный способ очистки весьма экономичен, благодаря относительно низкой стоимости гидроксида натрия, а также благодаря тому, что это вещество не оказывает практически никакого вредного воздействия на материалы теплообменных аппаратов, а значит, способствует продлению срока эксплуатации оборудования в целом (без необходимости ремонта).
К примеру, для чистки устройств теплообмена от масел, рыхлой ржавчины и других загрязнений готовится состав с содержанием 0,5-0,8%-ного раствора едкого натра и каких-либо щелочей. После окончания чистки контур устройства промывают 0,1-0,2 %-ным раствором гидроксида натрия для пассивации и нейтрализации внутренних поверхностей труб, а затем промывают их технической водой с уровнем рН на выходе, равным 6-7.
СОЛЯНАЯ КИСЛОТА
Самым эффективным способом считается химическое промывание ингибированным соляным раствором. Он применяется для стальных секционных и чугунных агрегатов. Заметим, что для очистки подбираются жидкости только с концентрацией 2-6%. На каждый 1 мм отложений концентрация увеличивается на 1%. Если накипь имеет толщину больше 6 мм, то химическая промывка водяного котла соляной кислотой производится в несколько заходов.
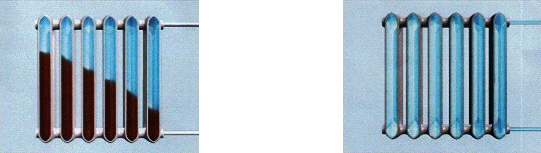
Промывка теплообменников ортофосфорной кислотой является простым и весьма эффективным способом промывки теплообменного оборудования без необходимости его разбора или осуществления каких-либо других процедур, усложняющих данный процесс. Существует множество разновидностей подобных реагентов, несколько отличающихся по степени эффективности воздействия на отложения, но очень схожих по составу.
Использование ортофосфорной кислоты для промывки теплообменников может давать отличные результаты, к тому же, такое средство не причиняет никакого ущерба пластинам теплообменного оборудования и даже создает особую защитную пленку, которая довольно длительное время препятствует пассивированию материалов, из которых состоит конструкция устройства.
Ортофосфорная кислота способна пассивировать (т. е. создавать защитную активную пленку) поверхность пластин и не влияет на уплотнитель.
Если Вы решили выбрать в качестве наиболее перспективного химический способ чистки, то для промывки теплообменника фосфорная кислота подойдет как нельзя лучше. Дело в том, что непрерывно циркулируя внутри контура аппарата, она полностью разрушает имеющиеся посторонние соединения, из которых состоит, к примеру, накипь или другие отложения, часто являющиеся причиной загрязнения внутренней поверхности устройства теплообмена. Вышеописанные составы необходимо подбирать в определенном процентном соотношении, информация о котором содержится на этикетке препарата.
Кроме того, при осуществлении процедуры промывки пластинчатых теплообменников составами на основе ортофосфорной кислоты желательно использовать специальные присадки, смягчающие вредное воздействие этих растворов на пластины и другие узлы конструкции теплообменного оборудования.
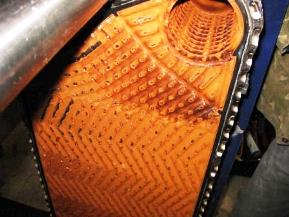
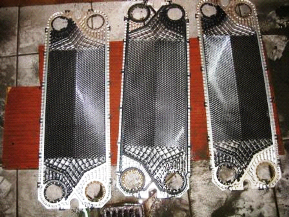
oil-diagnostic.ru
Промывка котлов сульфаминовой кислотой
В числе реагентов, используемых в процессе кислотной очистки, появляется всё большее количество эффективных составов, которые способны оказать помощь в удалении загрязнения с внутренней поверхности котельного оборудования. Одним из таких реагентов является сульфаминовая кислотная смесь. Она оказывается эффективной практически в любом случае, при этом не портит само оборудование, что делает её универсальным средством для промывки котлов самых разных типов.
Поскольку данная технология внедрена в практику относительно недавно, то и цены на такие услуги большинство компаний устанавливает более высокие. Наша организация пошла по иному пути. Уже сегодня кислотная промывка котлов сульфаминовой кислотой, осуществляемая нашими специалистами, доступна массовому клиенту. Мы смогли усовершенствовать технологию работы с данным веществом и теперь точно знаем, как сделать эту методику относительно недорогой и в то же время высокоэффективной. Отличные результаты показала промывка сульфаминовой кислотой водогрейных котлов КВР – после практически полного удаления загрязнений обследование аппаратуры показало полное отсутствие каких-либо повреждений внутренних поверхностей элементов отопления.
Все чаще находит своего заказчика и такая услуга, как промывка парового котла сульфаминовой кислотой. Наши специалисты делают всё необходимое, чтобы в конечном итоге добиться максимально возможной эффективности работы котельных устройств.
Особенности промывки котла сульфаминовой кислотой
Современная технология промывки котлов сульфаминовой кислотой имеет ряд особенностей. При проведении работ стоит учитывать, что:
- - очистка оборудования молокозаводов предусматривает необходимость удаления таких отложений, как молочный камень. В этом случае используется 1,5 -2% водный раствор, температура – 70-75 градусов, время выполнения промывочной операции – 40 минут;
- - для удаления отложений пивного камня на 10 -15 литров воды используют 0,5 – 1 кг кислотной составляющей, температура рабочей жидкости – 50-60 градусов;
- - удаление карбонатной накипи с поверхности элементов отопления осуществляется при температуре состава 70 -75 градусов, при этом промывка сульфаминовой кислотой котлов и других элементов аппаратуры должна проводиться составом 2-3% рабочей жидкости, состоящей из кислоты, воды и ингибиторов коррозии. Время проведения промывочной операции – до 7 часов.
www.teploobmennik.su
Кислотная промывка - Большая Энциклопедия Нефти и Газа, статья, страница 1
Кислотная промывка
Cтраница 1
Кислотные промывки также могут способствовать развитию трещин у нейтральных волокон гибов по их внутренней поверхности. Для ослабления вредного влияния промывки следует производить ингибированным раствором кислоты. [1]
Кислотная промывка и обработка комплексонами является ответственной операцией и должна выполняться специально подготовленным квалифицированным персоналом. [2]
Кислотная промывка и обработка комплексонами является ответственной операцией и должна выполняться специально подготовленным квалифицированным персоналом. Кислотную промывку ила обработку комплексен ами применяют на промышленных я водогрейных котлах только при сильном поражении их поверхности нагрева коррозией. [3]
Кислотная промывка предназначена для растворения и выноса из тракта окислов железа, окалины, отложений масла, мазута и пр. Кислотная промывка проводится при скорости движения промывочного раствора в недренируемых поверхностях 1 5 - 2 м / с, а в дренируемых 0 6 - 1 м / с. Для проведения кислотной промывки устанавливается специальный насос. Об окончании кислотной промывки судят по стабилизации содержания окислов железа в растворе на выходе из промываемого контура. [4]
Кислотная промывка производится раствором соляной, лимонной или другой кислоты. Для удаления ( выноса) ржавчины и окалины из котла необходима сильная циркуляция раствора кислоты, которая создается временными насосами с соответствующими трубопроводами. При прямоточных котлах производится одновременно промывка питательного тракта. Продолжительность проведения всего комплекса промывок современных мощных котлов составляет 15 - 30 дней. [5]
Кислотные промывки также могут способствовать развитию трещин у нейтральных волокон гибов по их внутренней поверхности. Для ослабления вредного влияния промывки следует производить ингибированным раствором кислоты. [6]
Кислотная промывка барабанных котлов 140 кгс / см2 производится по двухконтурной схеме. В первый контур, который промывается соляной кислотой, входит питательный тракт ( деаэратор 6 кгс / см2, питательные трубопроводы, ПВД), водяной экономайзер и экраны: во второй - пароперегреватель, который промывается обратным потоком в барабан гидразинно-кислотным раствором, моноцитратом аммония или адипиновой кислотой. На рис. 13 - 1 показана раздельная двухкоятурная схема соляно-хислотяой промывки барабанного котла с подводом моющих растворов к нижним коллекторам экранов. [7]
Кислотные промывки производятся в очень ограниченном размере и только под руководством опытного специалиста. Котлы с трещинами к кислотным промывкам не допускаются. [8]
Кислотные промывки могут способствовать развитию трещин у нейтральных волокон гибов по их внутренней поверхности. Для ослабления вредного влияния промывки следует производить ингибированным раствором кислоты. [9]
Кислотная промывка с принудительной циркуляцией осуществляется нижеследующим образом. В баке готовится, как указано выше, промывочный ингибированный кислотный раствор нужной концентрации и перекачивается насосом в очищаемый от накипи аппарат. Как только через трубу рециркуляции в бак начнет переливаться промывочный раствор, циркуляционный насос включают в постоянную работу. При этом, периодически отбирая пробы раствора, контролируют его концентрацию и в случае ее снижения добавляют в бак крепкой кислоты. Соответствующий объем отработавшей кислоты при этом сливается в дренаж. После прекращения выделения газа и стабилизации концентрации кислоты раствор ее из аппарата точно так же, как и в предыдущем случае, выпускают в дренаж, промывают аппарат водой и затем производят щелочение аппарата 1 % - ным раствором щелочи при циркуляции его в контуре бака в течение 6 - 8 час. По окончании щелочения аппарат снова промывают водой. [10]
Кислотные промывки должны, как правило, проводиться под наблюдением опытного химика. [11]
Кислотные промывки применяются также для очистки поверхностей нагрева барабанных и прямоточных котлов от отложений солей в процессе эксплуатации. При любом даже очень хорошем качестве питательной воды в определенных зонах пароводяного тракта происходит отложение солей. В результате ухудшается охлаждение стенок труб со стороны воды и пара, так как слой солевых отложений отличается низкой теплопроводностью. [12]
Кислотная промывка проводится без огневого подогрева в топке. [13]
Кислотная промывка котлов может производиться только лишь хорошо обученным персоналом под руководством квалифицированного специалиста. [14]
Кислотная промывка заключается в том, что в поверхности - нагрева котла насосом в определенной последовательности подаются различные растворы, основное назначение которых состоит в очистке внутренней поверхности труб от отложений ржавчины, окалины и других продуктов коррозии, а также от накипи. [15]
Страницы: 1 2 3 4
www.ngpedia.ru
ЩЕЛОЧЕНИЕ КОТЛОВ
Ремонт паровых котлов
После монтажа вновь установленного котла или окончания капитального ремонта внутренние поверхности его могут иметь окалину от сварки, ржавчину или масляные загрязнения. Перед пуском такого котла в работу необходимо предварительно произвести его щелочение— очистку внутренних поверхностей от загрязнений. Перед щелочением следует тщательно осмотреть внутренние и наружные поверхности котла.
Наружный осмотр производится с целью выяснения правильности сборки элементов котла и трубопроводов, устройства для регулирования и подачи воды, пара, топлива и воздуха, правильности установки контрольно-измерительных приборов и т. д.
Щелочение котла должно производиться в соответствии с «Инструкцией по щелочению паровых и водогрейных котлов», утвержденной Главтехуправлением Министерства энергетики и электрификации СССР 3 апреля 1970 г.
Наружный осмотр производится с целью выяснения правильности сборки элементов котла и трубопроводов, устройства для регулирования и подачи воды, пара, топлива и воздуха, правильности установки контрольно-измерительных приборов и т. д.
Перед началом щелочения котла необходимо осмотреть и промыть питательные баки, деаэраторы, питательные и вспомогательные трубопроводы.
Пароперегреватель, как правило, не подвергается щелочению и не заполняется щелочным раствором—от масляных загрязнений и ржавчины его очищают продувкой паром.
Заполнение котла водой и последующая подпитка при щелочении должны производиться химически очищенной питательной водой. Перед заполнением котла водой необходимо открыть вентиль для удаления воздуха, а там где его нет поднять один предохранительный клапан для удаления воздуха. Уровень воды в барабане доводится до нижнего предельного, после чего заполнение котла водой прекращается и поддерживается в течение всего процесса щелочения.
Щелочение сопровождается растопкой котла и подъемом давления.
Для обеспечения наибольшей эффективности при щелочении давление в котле необходимо довести до 75— 100 % рабочей величины, но не выше 1,3 МПа (13 кгс/см2) при поминальном давлении 1,4 МПа (14 кгс/см2) или 2,3 МПа (23 кгс/см2) при номинальном давлении 2,4 МПа (24 кгс/см2).
При щелочении следует производить огневой обогрев котл а.
При наличии парового прогрева нижнего барабана допускается комбинированный первоначальный разогрев котла огнем и паром до 0,4 МПа (4 кгс/см2). В дальнейшем должен производиться только огневой обогрев.
Реагенты вводятся в котел раздельно, в виде раствора через какой-либо штуцер верхнего барабана или фосфатными насосами. Ввод их в котел и сухом виде или не полностью растворившимися не допускается. В качестве реагентов применяют: едкий натр, тринатрийфос - фат и кальцинированную соду. Поэтому обслуживающий персонал, занятый работами по щелочению котла, должен быть обеспечен спецодеждой, защитными очками, перчатками и фартуками. Котельное помещение должно хорошо вентилироваться.
После заливки в него реагентов через каждые 3Д ч производится отбор проб котловой воды из верхнего и нижнего барабанов и камер экранов с целью определения ее щелочности и загрязненности.
Первоначальные небольшие продувки выполняют через 12—20 ч после качала щелочения, а наиболее интен-. сивные — к концу щелочения с целью удаления скопившейся грязи.
При обнаружении сильной загрязненности необходимо усилить продувку из нижних точек котла при давлении 0,5—0,6 МПа (5—6 кгс/см2). Щелочение котла, в зависимости от степени загрязненности внутренних поверхностей, продолжается в течение 48—86 ч, прекращают ее тогда, когда взятая проба воды окажется чистой. Режим щелочения выбирают в зависимости от загрязненности котла.
Если разрыв между окончанием щелочения и пуском котла превышает 10 дней, следует произвести консерва-
Таблица 3.6. Необходимое количество реагентов в единице объема котловой воды для щелочения котлов
|
Котлы новые с небольшим слоем ржавчины | |||
Е-2.5-14Р (КЕ-2.5-14С) | 20 | 30 | 12 |
Е-4-14Р (КЕ-4-14С) | 27 | 40 | 15 |
Е-6.5-14Р (КЕ-6,5-14С) | 35 | 52 | 21 |
Е-10-14Р (КЕ-10-14С) | |||
Е-10-24Р (КЕ-10-24С) | 48 | 72 | 29 |
Е-25-14Р (КЕ-25-14С) | |||
Е-25-24Р (КЕ-25-24С) | 80 | 120 | 47 |
Котлы новые с | Большим слоем ржавчины | ||
Е-2,5-14Р (КЕ-2.5-14С) | 32 | 48 | 20 |
Е-4-14Р (КЕ-4-14С) | 39 | 59 | 27 |
Е-6,5-14Р (КЕ-6,5-14С) | 56 | 84 | 35 |
Е-10-14Р (КЕ-10-14С) | |||
Е-10-24Р (КЕ-10-24С) | 76 | 115 | 48 |
Е-25-14Р (КЕ-25-14С) | |||
Е-25-24Р (КЕ-25-24С) | 127 | 190 | 80 |
Нию котла или перед пуском произвести вторичное щелочение.
Вода из котла после щелочения сливается с температурой не выше 50—60 °С при атмосферном давлении. Трубы котлов промывают через шланг горячей водой из барабана.
Необходимое количество реагентов в единице объема котловой воды для щелочения котлов приведено в табл. 3.6.
После щелочения и промывки составляют акт о состоянии внутренних поверхностей нагрева котла. Затем котел заполняют умягченной водой для испытаний на паровую плотность.
В течение первого месяца эксплуатации котла необходимо вести повышенную его продувку (примерно в два раза больше расчетной) для удаления загрязнений.
Котлы Е-1/9-1М, работающие на жидком топливе, оборудуются горелочными устройствами АР-90. Для защиты котла подача топлива автоматически прекращается при понижении уровня воды в котле ниже допустимого, при повышении давления пара в …
При изготовлении, монтаже и ремонте элементов котлов, пароперегревателей и экономайзеров должны применяться только стыковые соединения при сварке обечаек, труб (патрубков) и приварке выпуклых днищ, а также тавровые и угловые или …
А. Баранов
msd.com.ua