- 8 (495) 7487600
- 8 (495) 7487600
- 8 (925) 5552040
- 8 (925) 5552040
- Напишите нам
- Обратный звонок
Интернет магазин оборудования насосной, отопительной и водонагревательной техники №1
Производство водогрейных котлов от 1 до 10 МВт серии АКМЗ, водяных экономайзеров и трубных пучков для теплообменников. Котел тпп 804
Производство котла парового ТПП-312А
ООО "Асбестовский котельно-машиностроительный завод" производит котлы паровые ТПП-312А, а так же комплектующие для котлов.
Технические характеристики котла ТПП-312А:
- Типоразмер котла по ГОСТ - Пп-1000-25-545КЖ
- Температура подогрева воздуха, °C - 381
- Температура уходящих газов, °C - 165
- Температура питательной воды, °C - 260
- КПД, % - 89,5
- Тип воздухоподогревателя - регенеративный воздухоподогреватель РВП
- Вид топлива - каменный уголь (донецкий)
- Ширина, м - 39,3
- Глубина, м - 23,6
- Высота, м - 51,0
- Общая масса котла, т - 5200
- Масса поверхностей под давлением, т - 2420
- Масса легированной стали котла, т - 1342
- Масса аустенитной стали котла, т - 219
- Компановка котла - П-образная
- Регулирование температуры промежуточного перегрева - ППТО
Комплектующие для котла ТПП-312А:
- Радиационные поверхности нагрева, воспринимающие тепло от газов за счет излучения
- Конвективные поверхности нагрева
- Топочные камеры
- Топочные экраны, которые обеспечивают охлаждение стенок труб
- Горелки для котла
- Экономайзер для котла ТПП-312А
- Ширмовый пароперегреватель ТПП-312А, располагаемый в верхней части топки
Так же завод АКМЗ производит змеевик котла ТПП-312А, ширмы котла ТПП-312А, зоны максимальной теплоемкости и переходные зоны.
Удобные подъездные Ж/Д пути и развязки, а так же большая производственная территория завода обеспечивают возможность быстрой и качественной сборки котла ТПП-312А из отдельных произведенных элементов, с последующей погрузкой в Ж/Д вагоны и отправкой заказчику.
akmz.net
Модернизированные схемы подвода газа к горелкам с использованием газооборудования ЗАО. Обвязка двухканальных по газу горелок, страница 4
Котёл |
Теплонапряже-ние топочного объема, ккал/(м ■ ч) |
Dmm, т/ч |
Число горелок/число газовых каналов |
Число ярусов |
Компоновка горелок |
Подвод воздуха к горелкам |
Поставщик газового оборудования |
ПК-41 |
358 • 103 |
475 |
6/1 |
1 |
Фронтовой и задний экраны |
Индивидуальный воздуховод |
АМАКС |
ТГМП-314 |
167 • 103 |
950 |
16/2 |
2 |
То же |
АМАКС |
|
ТГМП-204ХЛ |
199 • 10J |
2650 |
36/1 |
3 |
"" |
Общий короб |
АМАКС |
ТПП-804 |
64 • 103 |
2650 |
24/2 |
2 |
a i» |
По импорту |
|
ТГ-104 |
181 ■ 103 |
670 |
12/2 |
2 |
Фронтовой экран |
Индивидуальный воздуховод |
АМАКС |
ТГМЕ-206 |
196,1 |
670 |
12/2 |
2 |
Задний экран |
АТЭК |
|
ТГМП-114 |
232 |
475 |
6/3 |
1 |
Фронтовой и задний экраны |
АТЭК |
|М<
[оваленко А. Л., инженеры
В связи с разработкой "Правил безопасности в
газовом хозяйстве" ПБ 12-245-98 и "Правил безопасности систем газораспределения" ПБ 12-529-03 (далее по
тексту Правила) многие электростанции приступили к модернизации существующих
проектных схем газоснабжения котлов. В проектных схемах, как правило,
последовательно перед каждой горелкой располагались задвижка с электроприводом
и задвижка с ручным или электрическим приводом. В качестве примера на рис. 1
показаны схемы газоснабжения котлов ПК-41, ТТМП-204ХЛ, ТГ-104, разработанные
более 30 лет назад. Розжиг горелок производился от стационарных запальных
устройств (ЗУ) или переносными газовыми запальниками. Селективный контроль
факела каждой горелки проектом не предусматривался. Была предусмотрена только
защита по погасанию общего факела в топке.
В двух- и трёхканальных горелках выделялся растопочный канал с расходом
газа 20 - 30% номинального.
Правила требуют установки перед каждой горелкой последовательно двух быстродействующих ПЗК или одного ПЗК и одной задвижки с электроприводом. В обоих случаях перед последним по ходу газа запорным устройством должен быть предусмотрен трубопровод безопасности диаметром не менее 20 мм, оснащённый запорным устройством с электроприводом.
Согласно Правилам все горелки котла должны быть оснащены ЗЗУ, обеспечивающими режим
|
|
|
ЗЗУ
12
&£—&£—
Рис.
1. Проектные схемы подвода газа к горелкам:
а - Ириклинская ГРЭС-1, котёл ПК-41; б - Сургутская ГРЭС-2, котёл ТГМП-204ХЛ; в - Сургутская ГРЭС-1, котёл ТГ-104; г -Пермская ГРЭС, котёл ТПП-804; 1,4- клапан электромагнитный и пневматический отсечной соответственно; 2, 3 - задвижка ручная и электрифицированная соответственно
-!ПРЙЙ!!!1ГШ»Г рй'Я'М
vunivere.ru
Каркас котла
Каркас котла
Каркас котла - пространственная рамная металлоконструкция, предназначенная для крепления (опоры или подвески) поверхностей нагрева и трубопроводов, ограждений, изоляции, площадок обслуживания и других элементов котла и вспомогательного оборудования. Он состоит из вертикальных колонн 1, горизонтальных балок 3, горизонтальных и вертикальных ферм 2, из связей-раскосов 4 и упрочненной конструкции потолочного перекрытия (рис. 87). Колонны 1 крупных котлов изготовляют из сварных профильных балок большого размера. Сварными делают основные балки 3 потолочного перекрытия и некоторые другие горизонтальные балки. Раскосы, фермы - это профильный прокат (швеллер, двутавр), связанный между собой (сваренный) накладками 6.
Горизонтальные фермы 2 и балки так же как и связи-раскосы 4 применяют для придания поперечной устойчивости колоннам и повышения жесткости каркаса. Они могут также воспринимать нагрузки, возникающие при повышении (или колебании) давления в топке и газоходах. Основные колонны каркаса располагают по углам топочной камеры и конвективной шахты, а промежуточные вдоль стен. Число последних зависит от мощности котла. При близком расположении к топке конвективной шахты или на облегченных конструкциях конвективной шахты внутренние колонны не ставят, как например, на котлах (Пп = 1000-25-545/545 КТ (ТПП-210А).
В котлах, опирающихся на собственный каркас, для уменьшения удельной нагрузки на фундамент под колонны устанавливают опорные башмаки 5, состоящие из опорных плит и ребер жесткости. Для уменьшения термических напряжений в каркасе основные несущие его элементы располагают за пределами газоходов и их обмуровки. Сочленение обогреваемых балок, например, опорных балок поверхностей нагрева конвективной шахты с балками каркаса выполняют в виде скользящей опоры с одной стороны при неподвижном креплении с другой. К каркасу котла крепят помосты и лестницы, необходимые для обслуживания и ремонта котла, его узлов и оборудования. Лестницы и помосты являются дополнительными поперечными и диагональными связями, и их обычно также относят к элементам каркаса. Их выполняют из рам, сваренных из швеллеров и уголков, покрытых просечно-вытяжным или рифленым листом.
Во многих котлах часть поверхностей нагрева и топки подвешивают к потолочному перекрытию. В этих случаях основные несущие (хребтовые) балки сваривают из толстых листов, а трубы экранов или газоходов связывают поясами жесткости 2 (см. рис.45). Шарнирное соединение балок поясов жесткости с трубами 1 и 3 и между собой (в углах) обеспечивает линейное перемещение вдоль балок экранов при тепловом их удлинении. Котлы мощных энергоблоков, например, Пп-3650 - 25-545/545-ГМ (ТГМП-1202), Пп-2650-25-545/545-ГМ (ТГМП-204), Пп-2650-25-545/545-КТ (ТПП-804) начали выпускать без собственного опорного каркаса. Котел с площадками, лестницами и некоторым оборудованием подвешен на потолочном перекрытии, опирающемся нй металлоконструкцию здания. Такое решение стало возможным благодаря использованию газоплотных мембранных панелей и облегченной обмуровки. Потолочное перекрытие здания, воспринимающее все нагрузки, выполняют из нескольких мощных хребтовых балок значительного сечения и высоты (до 7 м), и связывают поперечными балками меньшего размера. Такую систему связи мощных балок называют жестким диском.
Хребтовые балки в зависимости от соотношения размеров котла могут быть расположены продольно или поперечно. Для придания жесткости стенам топки, восприятия нагрузок от наддува, от повышения давления при хлопках, а также с целью предупреждения деформации экранов предусматривают обвязочный каркас котла с горизонтальными поясами жесткости через 2,5-3 м по высоте. К нему крепят помосты и лестницы. Совмещением каркасов котла и здания удается снизить металлоемкость конструкций. На некоторых прямоточных котлах применяют щитовой каркас, опирающийся на портал, поднимающийся до отметки обслуживания котла. Поверхности нагрева собирают вместе с вертикальными щитами, включающими элементы каркаса. На верхний ряд щитов устанавливают потолочное перекрытие.
Опорные конструкции котла являются важнейшими его элементами, обеспечивающими безопасность эксплуатации всей ТЭС. При проектировании необходимо учитывать все виды нагрузок, воздействующие на них (постоянные и переменные). К постоянно действующим нагрузкам относят нагрузки от массы поверхностей нагрева, трубопроводов (барабанов) и заполняющей их среды, изоляции, обмуровки, пылегазовоздухопроводов, опирающихся на каркас, некоторых видов оборудования, устройств обдувки и очистки поверхностей нагрева. К переменным нагрузкам относят длительные, кратковременные и особые.
В процессе работы котла на каркас котла длительно действуют нагрузки от термических напряжений, частично от давления среды (например, на опоры трубопроводов и др.), массы шлака в топке, загрязнений на поверхностях нагрева, золы и дроби в системе золоулавливания (опирающейся на каркас). Кроме того, кратковременно могут сказываться ветровые и снеговые нагрузки, присутствие людей и наличие материалов на помостах и др. К особым нагрузкам относят сейсмические нагрузки, дополнительные нагрузки на каркас котла при монтаже оборудования и др. Определив нагрузки и их распределение, рассчитывают каркас котла как пространственную рамную конструкцию из балок.
kotel-kv-300.ru
Пермская ГРЭС - энергетическое сердце Пермского края!


Мы от лица нашего журнала поздравляем ВАС с этим событием! С ДНЕМ ЭНЕРГЕТИКА! И пусть у Вас все будет супер-пупер!
Мы в свою очередь будем тоже Вам помогать, рассказывать и популизировать отрасль на наших страницах. И именно сегодня, дорогие наши читатели, мы расскажем в рамках нашего проекта "Пермский край - нам есть чем гордиться!" об еще одной гордости Пермского края - Пермской ГРЭС!
Пермская ГРЭС расположена в 5 км северо-западнее города Добрянка Пермского края, на левом берегу Камского водохранилища. Она является крупнейшим поставщиком электроэнергии, четвёртой по мощности электростанцией в Уральском регионе. На её долю приходится почти 40% энергомощностей Пермского края, она является самой крупной электростанцией Прикамья и может обеспечивать более 50% потребностей региона в электроэнергии. Установленная электрическая мощность станции составляет 2 400 МВт, а установленная тепловая мощность - 620 Гкал/ч. В 2012 году она выработала 13 042,949 млн КВТ.ч и отпустила тепла 296,798 тыс. ГКал. Электростанция введена в эксплуатацию 30 июня 1986 г. Топливом для нее является природный газ Уренгойского и Ямбургского месторождений, поступающий на электростанцию по ответвлениям от магистральных газопроводов.
Пермская ГРЭС входит в Группу «ИНТЕР РАО ЕЭС» и является с 1 октября 2012 года филиалом ОАО «ИНТЕР РАО - Электрогенерация» http://www.irao-generation.ru/ .
ОАО «Интер РАО-Электрогенерация» является 100%-ной дочерней компанией ОАО «ИНТЕР РАО ЕЭС». В состав ОАО «ИНТЕР РАО - Электрогенерация» входят 16 крупнейших тепловых электростанций России общей установленной электрической мощностью свыше 21 ГВт. Функции единоличного исполнительного органа ОАО «Интер РАО-Электрогенерация» исполняет управляющая компания - ООО «Интер РАО-Управление электрогенерацией».
Группа ОАО «ИНТЕР РАО ЕЭС» http://www.interrao.ru/ – диверсифицированный энергетический холдинг, присутствующий в различных сегментах электроэнергетической отрасли в России и за рубежом. Компания занимает лидирующие позиции в России в области экспорта-импорта электроэнергии, активно наращивает присутствие в сегментах генерации и сбыта, а также развивает новые направления бизнеса. Установленная мощность электростанций, входящих в состав Группы «ИНТЕР РАО ЕЭС» и находящихся под её управлением составляет более 33,5 ГВт.
2.
В настоящее время электроэнергия, вырабатываемая Пермской ГРЭС, в северном направлении поступает в Березниковско - Соликамский промышленный узел, в восточном направлении - в центр Свердловской области и в западном направлении - в Пермско–Закамский энергоузел, граничащий с двумя промышленными регионами: Удмуртской республикой и Республикой Башкортостан.
3. А вот и главная проходная. Вперед, друзья...
4. На проходной располагается вот такой крутящийся шар, символизирующий движение, жизнь, энергию..
5. В режиме реального времени мы можем наблюдать результаты работы добрянских энергетиков
Предлагаю начать наше знакомство с "сердцем" электростанции - с центральным щитом управления (ЦЩУ). Помимо него на ГРЭС есть еще и 2 БЩУ (блочный щит управления). ЦЩУ - это главное центральное помещение, где сосредоточены основные средства контроля и управления. Он связан с местными щитами, всем оборудованием, расположенным на территории ГРЭС, системой контрольных кабелей. Здесь происходят процессы управления основным и вспомогательным оборудованием, обеспечивается связь с Системным оператором. По заданию РДУ СО (Региональное диспетчерское управление Системного оператора) происходит регулирование мощности электростанции и нагрузки энергоблоков.
6. ЦЩУ (центральный щит управления)
7.
8.
9.
Попадая на крупные промышленные объекты, мы чаще всего не замечаем некоторых технологических процессов, происходящих внутри организации, различные лаборатории...Конечно трубы, агрегаты, промстроения - они все снаружи и впечатляют своими масштабами и индустриальной красотой. Но для энергетики - постоянный мониторинг воды, масел и других веществ очень актуален и важен, а так как мы хотели все посмотреть, то не смогли пройти мимо лаборатории.
10. Лаборатории масла и топлива
На Пермской ГРЭС внедрена и постоянно совершенствуется автоматизированная система химического контроля и управления водно-химическим режимом, которая включает три основные части:
- узел подготовки проб,- комплект анализаторов,- информационно-вычислительный комплекс.
Надежность подготовки проб обеспечивается двухступенчатым охлаждением, а также защитой проб, подаваемых на датчики анализаторов, от превышения давления и температуры.
11. Центральная химическая лаборатория
Приборы автоматического химического контроля представлены иностранными фирмами, а также российским производителем и установлены в наиболее ответственных местах паро-конденсатного тракта энергоблоков, химводоочистки и схемах подпиточной воды.
Энергоблоки работают в кислородно-аммиачном водном режиме. Регулирование дозирования аммиачного раствора производится дистанционно или автоматически лаборантами из экспресс-лаборатории.
В 2010 году проведена реконструкция схемы подачи газообразного кислорода в конденсатный тракт энергоблоков, теперь дозировка кислорода может осуществляться в автоматическом и дистанционном режиме управления. Автоматизация данного процесса дает большие возможности для обеспечения и поддержания ВХР на высоком уровне.
12.
Оперативный химический контроль осуществляется сменными лаборантами в экспресс-лабораториях с применением автоматических приборов и быстрых методов химического анализа, выполняемых вручную. Периодический химический контроль осуществляется персоналом центральной химической лаборатории (ЦХЛ). Этот вид контроля построен на применении достаточно точных методов анализа с использованием уникальных, лабораторных приборов.
13.
На основании показаний химконтроля энергетических масел решается вопрос о пригодности масла к эксплуатации, необходимости его очистки или замены, также делается вывод о неисправностях маслонаполненного оборудования.
14.
15. А вот по этим трубочкам и бегут пробы для анализа...
Далее переходим в Химический цех:
16. Общий вид химического цеха
17.
18.
19.
20.
21.
22. Оперативный щит химводоочистки. Рабочее место оператора щита.
23. А вот и общий вид машинного зала котлотурбинного цеха.
24. Испарительная установка
Как я писал выше, основным топливом для нашей станции является газ. Он, попадая на станцию, проходит ряд ступеней. На подходе к ГРЭС его давление понижается первоначально с 70 атмосфер до 12, а затем, поступая уже во владения специалистов котлотурбинного цеха электростанции, снижается на ее газораспределительных пунктах до 2 атмосфер. По трубам, которых большое количество здесь, голубое топливо поступает в горелки. Там, при соблюдении жесточайших пропорций, он смешивается с воздухом и воспламеняется, достигая в топках огромной температуры в 1 800-2 000 градусов Цельсия. Здесь-то и происходит встреча огня и находящейся за стальными стенками паропроводов воды.
Проходя по тракту котла, вода нагревается и превращается в перегретый пар, обладающий невероятными показателями: давление - 240 атмосфер, температура - 545 градусов С.
Дальнейший его путь лежит в паровую турбину, где он вращает ротор турбины и генератора со скоростью 3 тысячи оборотов в минуту. В результате, в статоре возникает электрический ток. Далее эта энергия поступает на трансформатор и, увеличиваясь там с 20 тыс. вольт до 200-500 тысяч вольт, мощным потоком перетекает на открытое распределительное устройство и устремляется по линиям электропередач к потребителям. Вот так вкратце и выглядит процесс производства электроэнергии на ГРЭС.
25. Один из трех турбоагрегатов
Перечень основного оборудования энергоблоков 800 МВт на Пермской ГРЭС:
- паровой котел ТПП-804: 2650т пара в час, 25,5/4,0 МПа, 545/542ºС, завод-изготовитель – ОАО «Таганрогский котельный завод», г. Таганрог;- турбина: К-800-240-5, завод-изготовитель – ОАО «Ленинградский металлический завод», г. Санкт Петербург;- генератор Т3В-800 2УЗ, с полным водяным охлаждением, завод - изготовитель – ОАО « Электросила», г. Санкт Петербург;- силовой трансформатор 1000 МВА, 24/220 (500) кВ, завод-изготовитель – Запорожский трансформаторный завод, г.Запорожье, Украина.
26. Турбогенератор ТГ-1
Сейчас на станции работает три энергоблока по 800 МВт. Первый энергоблок введён в эксплуатацию 30 июня 1986 году, второй – 28 декабря 1987 году, третий – 30 марта 1990 года.
27. Турбоагрегат
28. Паропроводы энергоблока
В марте 2013 года Группа «Интер РАО» приступила к строительству четвертого парогазового энергоблока (ПГУ) на Пермской ГРЭС установленной мощностью 800 МВт. Ввод энергоблока в эксплуатацию запланирован на декабрь 2015 года. Стоимость строительства оценивается в 30 млрд руб. По сути это один из крупнейших инвестиционных проектов в Уральском регионе сегодня и это очень радует.
29. Турбогенератор
На новом 4-ом энергоблоке будет установлено парогазовое оборудование производства фирмы «Сименс» (паровая турбина, две газовых турбины, три электрогенератора), соответствующее самым строгим стандартам экологической безопасности и обладающее одним из самых высоких в отрасли КПД – 57-58%.
Основное оборудование 4-го энергоблока:
• Паровая турбина SST5-5000 мощностью 290 МВт, производитель Siemens;• Две газовых турбины SGT5-4000F мощностью 292 МВт каждая, производитель Siemens;• Три электрогенератора SGen5-1000А мощностью 165-350 МВА, производитель Siemens;
30.
С вводом в эксплуатацию энергоблока №4 Пермская ГРЭС увеличит установленную мощность до 3 200 МВт и войдёт в пятерку крупнейших теплоэлектростанций России. Планируемый показатель выработки электроэнергии будет достигать 18-19 млрд. кВтч.
31.
Ввод в эксплуатацию четвёртого энергоблока обеспечит растущую потребность в энергии крупнейшие предприятия региона.
32.
33. А вот это блочный щит управления (БЩУ) - основной пост оперативного управления энергоблока, где дежурит оперативный персонал, ведущий эксплуатацию электростанции. С БЩУ производится управление всем оборудованием, входящим в состав энергоблока и всеми вспомогательными системами и механизмами. Оперативный персонал, пользуясь оперативной связью и личным осмотром, следит за надежной работой всего оборудования.
34. Рабочее место старшего машиниста энергоблока и инженера-электроника.
35. Рабочее место машиниста энергоблока по котлу.
36. Рабочее место машиниста энергоблока по турбине.
37.
38.
39.
40. Блочный щит управления № 2.
41.
42. Масштабы станции, конечно, впечатляют - высота более 100 метров, сейчас мы попробуем подняться выше...
43. Переплетение труб по всей станции создает интересные образы...
44. Поднялись
45. Хребтовые балки котлоагрегата.
46. Оцените высоту сами...
Пермская ГРЭС расположена на берегу Камского водохранилища. И это не случайно. Электростанция потребляет огромное количество воды. Она поступает из Камы по специальному подводящему каналу и, прежде чем попасть в систему трубопроводов котла, подвергается самой тщательной подготовке в химическом цехе электростанции. А вот там, вдалеке, виднеется и сам город Добрянка - "Маленькая или Уральская Венеция", именно так ее называют местные жители. И это не удивительно, ведь она практически со всех сторон окружена речками, прудом и заливом.
47. Вид сверху на Каму и отводящий канал.
48.
Пройдя в химцехе технологический цикл, вода лишается всех ненужных примесей, и становится дистиллированной. Не будь этого, на стенках трубопроводов регулярно возникали бы опасные тромбы в виде слоя накипи. Сейчас же вода, применяемая на Пермской ГРЭС, настолько чиста, что здесь давно уже отказались от экологически вредных кислотных промывок котлов. Водно-химический режим на добрянской электростанции - один из самых лучших в отрасли.
49.
50. Масимальная отметка котельного отделения.
51. Горелочные устройства котлоагрегата.
52. Подогреватели технической воды.
53. Пробоотборные точки испарительной установки.
54. Котельное отделение.
55. Насосный парк сетевой воды.
56. Индивидуальные средства защиты слуха - беруши.
57. Основной силовой трансформатор
Пермская ГРЭС всегда шла в ногу со временем и даже опережала, внедряла новые ноу-хао и становилась примером для отрасли. Уровень автоматизации технологических процессов всегда был на высоте. Именно здесь впервые в отечественной энергетике заработал цех автоматических систем управления тепловыми процессами (АСУ ТП).
58.
59. Объединенное распределительное устройство 220-500 кВ (ОРУ-220, 500)
60.
Вот, собственно, и все на сегодня! О Пермской ГРЭС можно рассказывать и рассказывать, и мы обязательно постараемся это делать, тем более, что нас обещали пригласить еще. Нам очень понравилось, что идут положительные качественные изменения, станция увеличивает свои мощности, она информационно открыта, умеет работать не только с традиционными СМИ, но и с блогосферой! Вот Вам пример лидера, учитесь!
Еще раз поздравляем с профессиональным праздником! И хотим поблагодарить за теплый прием:
Марковскую Марину - начальника сектора СО и СМИ филиала «Пермская ГРЭС» ОАО «ИНТЕР РАО – Электрогенерация»;Кравченко Ольгу - специалиста производственно-технического отдела
Музей Пермской ГРЭС: http://zavodfoto.livejournal.com/1815141.html
yablor.ru
Трубы оребренные, спирально-ленточное оребрение труб
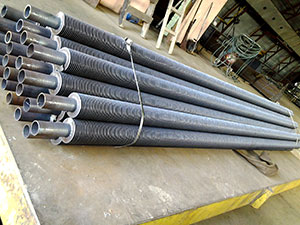
ООО "Асбестовский котельно-машиностроительный завод" производит трубы со спирально-ленточным оребрением.
Оребренные трубы предназначены для использования в теплообменниках воздушно-водяной и воздушно-маслянной систем электрических машин и трансформаторов общего назначения.
Все конструкции теплообменных оребренных труб защищены авторскими свидетельствами.
Оребренная труба изготавливаются без защитного покрытия длинной до 6 м, а для тропического климата с защитным анодно-окисным покрытием, длиной до 2,5 м.
Оребрение производится методом прикорневой приварки ленты непрерывным швом с использованием ТВЧ.
Преимущества оребренных труб:
- Коэффициент теплопередачи увеличивается до 50%
- Расход труб сокращается до 50%
- Общий вес теплообменников снижается на 30-40%
- Ресурс работы поверхности нагрева увеличивается в 2-3 раза за счет снижения скорости в шахтах и уменьшается абразивный износ
- Уменьшение на 20-25% аэродинамического сопротивления за счет снижения скорости дымовых газов
- Снижение температуры дымовых газов за счет увеличения поверхности нагрева без расширения шахты
Применение оребренных труб
- теплообменники
- теплоутилизаторы
- подогреватели
- экономайзеры
- калориферы
- конденсаторы воздушного охлаждения
- энергетическая промышленность
- химическая промышленность
- нефтеперерабатывающая промышленность
Для оребрения труб используются трубы и лента из углеродистой, низколегированной и аустенитной стали, которая приваривается непрерывным швом с использованием ТВЧ.
Рекомендуемые размеры ленты для оребрения труб
Углеродистая, низколегированная и легированная сталь: 1*11; 1*12; 1*15; 1,3*17; 1,5*20Высоколегированная сталь: 0,8*10; 1,25*12; 1,3*12; 1,3*15
Рекомендуемые сочетания марок стали трубы и ленты для оребрения
Марка ленты | Марка трубы |
08КП, 08ПС | 10, 20, 09Г2С, 10Г2, 12Х1МФ, 12МХ, 15ХМ |
08Х18Н10 | 08Х18Н10Т, 08Х18Н12Т, 12Х18Н10Т, 12Х18Н12Т |
|
h - высота ребраt - шаг оребренияb - толщина ребраS - толщина стенки трубыd - диаметр трубыD - диаметр оребренной трубы (общий) |
Для оребрения используются труба и лента из углеродистой, низколегированной и аустенитной стали, которая приваривается контактным способом.
Оребренная труба может использоваться в теплообменниках (теплоутилизаторах, котлах-утилизаторах подогревателях, экономайзерах, калориферах, конденсаторах воздушного охлаждения, продуктовых змеевиках нагревательных печей, батареях отопления) в энергетике, химической, нефтеперерабатывающей и других отраслях промышленности.
Вся выпускаемая продукция заводом "АКМЗ" соответствует государственным стандартам и техническим условиям.
Уточнить условия изготовления трубопроводов и паропроводов, а так же сформировать заказ Вы можете, обратившись к специалистам нашей компании.
akmz.net